Inverted-U Systems Protect Workers at Aircraft Fueling Station
Products used
Overview
Pharr Better Solutions is an industrial solutions supplier and a Spanco and Rigid Lifelines dealer based in Austin, Texas. Marty Rigby at Pharr Better Solutions took on a local fall protection job for a company with a fleet of corporate private aircraft.
The facility includes a fueling station near the tarmac. The fueling station consists of four 35-foot long fuel tanks that are filled and used to fuel the company’s aircraft. Periodically, workers have to climb on top of the fuel tanks to check the fuel levels and to refill the tanks when needed.
While on top of the fuel tanks, workers are exposed to potential fall hazards. The tops of the tanks are 12 feet, six inches high, which is well over the four foot OSHA requirement for fall protection in General Industry applications (OSHA 1910.28(b)(1)(i)). The company needed to implement safety equipment to comply with that requirement and to provide adequate protection to their workers.
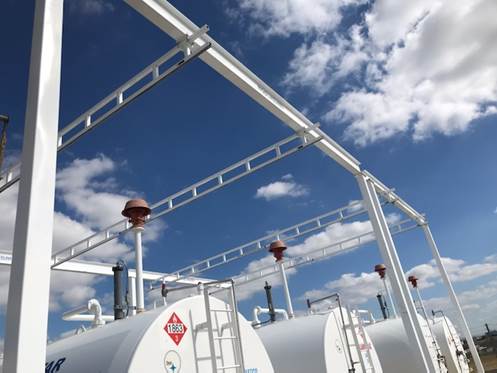
Solution
Pharr Better Solutions and Rigid Lifelines worked together to find the right solution to meet all of the needs of the application. One of those needs was a low headroom requirement. Because the system is located near air traffic, the system needed to be as low as possible.
Marty explained that they looked at the possibility of using a Rigid Lifelines Traveling Bridge Fall Protection System, which could provide the necessary worker capacity and coverage for the fueling area. However, this system type would have created a greater overall height than they wanted.
Instead, they decided to implement two Rigid Lifelines Inverted-U Fall Protection Systems with two monorails each. Each monorail is 40 feet, eight inches long with a Trolley-Hook Height of 20 feet. The four monorails are positioned above the four fuel tanks to provide access along the full length of the tanks. The Inverted-U design allows the system to achieve the same Trolley-Hook Height as the Traveling Bridge with a lower overall height. Fully assembled, the system had an overall height of 23 feet, six inches, which met the goal of keeping the entire project under 25 feet tall.
The systems also required a custom footing to mount in position. The fuel tanks are located within a containment basin on a concrete slab that couldn’t be penetrated for anchoring the system. A local engineering firm designed special galvanized steel base plates to provide sufficient anchorage. Pharr Better Solutions fabricated the steel baseplates, which were then mounted on the concrete.
Impact
The new Rigid Lifelines system provides complete coverage over all of the fuel tanks. The two Inverted-U systems and four total monorails allows four workers to access all four tanks at the same time if necessary. As Marty explained, this system was the simplest way to meet the end user’s needs.
Marty also explained that Pharr Better Solutions has had a long relationship with both Spanco and Rigid Lifelines. As a Spanco dealer, they have been selling and installing material handling systems for more than 20 years. When Spanco developed the Rigid Lifelines division, their good relationship with the company meant Pharr Better Solutions began selling fall protection systems as well. Since then, they have continued to sell and install many Rigid Lifelines fall protection systems throughout Texas.