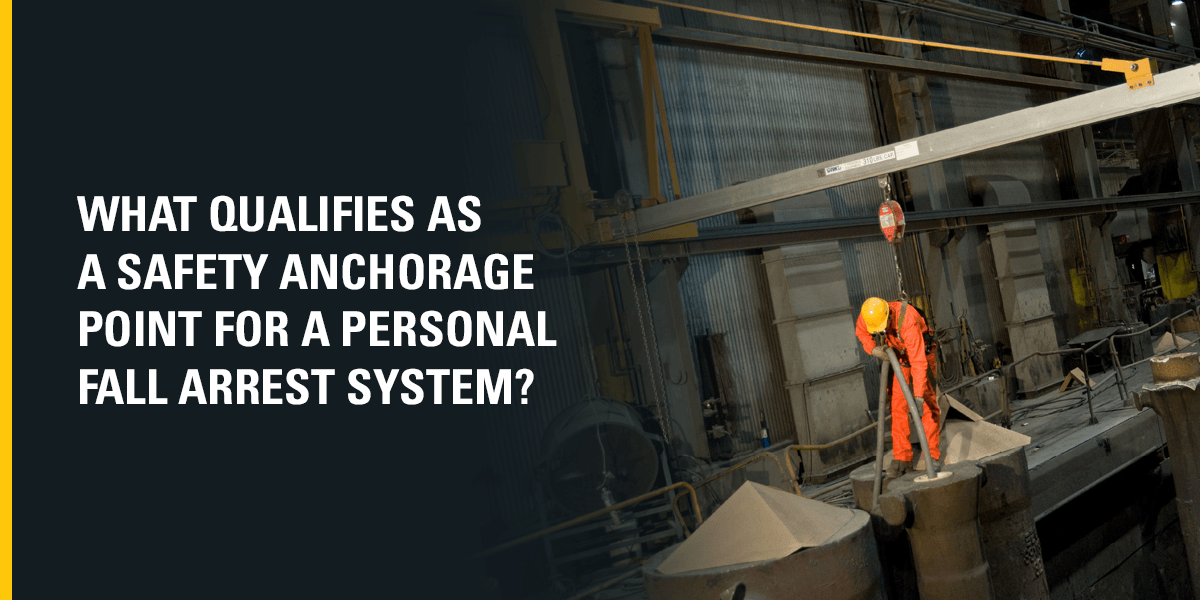
What Qualifies as a Safety Anchorage Point For a Personal Fall Arrest System?
January 28, 2022
Personal fall protection systems require strong components to protect workers from fall hazards, so it is crucial to select an appropriate anchor point. However, you may not know how to tell whether an anchor point is suitable. Below, we’ll define what an anchor point is, examine OSHA fall protection regulations, and discuss how to select the right anchor point for different jobs.
What Is an Anchorage for Fall Protection?
An anchorage is a secure attachment for workers to connect self-retracting lanyards or lifelines via a body harness for fall arrest or fall restraint purposes. An anchorage can be a complete engineered system designed specifically for fall protection or a secure connection point on an existing structure. Whether an anchorage is engineered or not, its strength depends on its design, condition, orientation relative to the loading direction, and how it connects to the supporting structure.
The Occupational Safety and Health Administration (OSHA) standard 1910.140(c)(13) states that anchorages must be “capable of supporting at least 5,000 pounds (22.2 kN) per employee attached; or designed, installed, and used, under the supervision of qualified person, as part of a complete personal fall protection system that maintains a safety factor of at least two.”
Let’s look at the “5,000 pounds” requirement first. This part of the standard refers to non-engineered anchorage points that have not been installed or certified by a Qualified Person as defined by OSHA. Under this requirement, an OSHA-defined Competent Person can determine the safety of a potential anchorage point by examining it and concluding whether it can support a weight of 5,000 pounds. This kind of determination is typically an estimation; it is nearly impossible to know exactly how much force a structure can withstand from observation. The safer option is to use an engineered anchorage.
The second part of the standard is relevant to professionals who design and install engineered fall protection systems. A person who meets the OSHA and ANSI Z359 definitions of a qualified person should be able to design a complete engineered fall protection system with a safety factor of two to meet the OSHA requirement.
The safety factor of two can be understood by examining more of OSHA’s fall arrest standards. OSHA 1910.140(d) requires engineered fall arrest systems to limit the force applied to a worker when arresting a fall to a maximum of 1,800 pounds. This value is known as the Maximum Arresting Force or MAF. To meet the requirement for a safety factor of two, the anchor point provided by the engineered system must be able to support a load of 3,600 pounds—two times the MAF.
Importance of Anchor Point Strength and Stability

Around one-third of the deaths in the construction industry are due to workers falling to a lower level. While fall arrest systems are effective at keeping crews safer, their anchor points must be secure enough to arrest a worker’s motion if they fall while working at height. If an anchorage point lacks strength or stability, it may not hold the combination of the worker’s weight and the force of their fall.
For this reason, tugging and pulling the anchor is inadequate for determining whether it will function as intended. Ensuring your fall protection anchor points can support twice the MAF confirms your system can effectively arrest a worker’s fall.
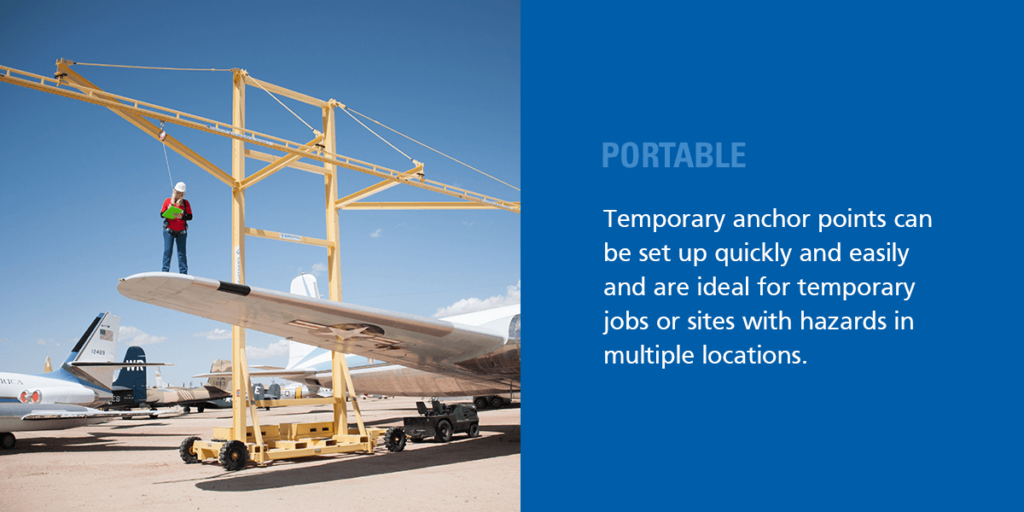
What Are the Different Types of Anchor Points?
Anchor points can be either engineered or non-engineered. Engineered anchor points can be either permanent or portable to suit the needs of different situations.
- Non-Engineered: Non-engineered anchors are not designed by a qualified person. These anchor points may include attachment points installed specifically for fall protection or existing structural components used for connecting fall protection lanyards and harnesses. These anchor points must meet the OSHA 5,000-pound requirement and must be carefully examined before use.
- Engineered: Engineered anchor points are designed and installed specifically for fall protection and meet the requirement for a safety factor of two.
- Permanent: As their name suggests, you cannot move permanent anchor points. They’re fixed permanently in place and used by crews who regularly work at heights. These anchor points include engineered fall restraint and fall arrest systems, such as Rigid Lifelines Traveling Bridge or Swing Arm Anchor TrackTM systems.
- Portable: Portable anchor points can be set up quickly and easily and are ideal for temporary jobs or sites with hazards in multiple locations. These anchor points can include structures that can be removed without damaging the supports or mobile systems, such as the Rigid Lifelines Griffin or Rolling A-Frame systems.
Permanent vs. Temporary Anchor Points
When you choose an engineered system, you must select permanent or temporary anchor points.
Many structures feature permanent anchor points for fall protection systems, from high-rise buildings to homes. These reusable options require regular inspections, but their easy, one-time installation makes them a cost-effective choice, especially when jobs after the construction phase would require crews to use fall protection systems while working at height.
Temporary anchor points do not penetrate the building. Instead, workers affix them using system-specific instructions that may involve nails, slings, beam clamps, or other fasteners. Crews can move these anchorage points as needed and remove them when the work is complete. Some structures may be unable to accommodate permanent anchor points, making temporary solutions essential.
Consider your application and the structure’s requirements, such as roofing materials. For example, permanent anchor points are necessary for concrete roofs, while temporary systems are common for metal roofing.
How Should You Choose an Anchor Point?
When choosing a fall protection anchorage, it’s best to start by looking at the safest options first. If an engineered system is available, it should be used over any non-engineered anchor point. If non-engineered anchor points are the only available options, start with the strongest material, such as a steel member. A wood member can offer a viable option, but it must be certified by someone who knows or can determine the load capacity of the member. Additionally, any anchor bolts, through-bolts, and plate washers, eyebolts, turnbuckles, embeds, or beam clamps must be inspected and approved by a competent person before it can be used as an anchor point.
Finally, always avoid known unsafe anchor points that are likely to fail during a fall event. Never use any of the following as anchorage points:
- Standard guardrails and railings
- Ladders, rungs, and scaffolding
- Light fixtures
- Plumbing
- Conduit and wiring harnesses
- Ductwork and pipe vents
- Rebar
- Lanyards
- Vents and fans
- Roof stacks
Further, you should never use structures or items that fail to meet OSHA standards. Rely on personal fall protection system manufacturers to answer your questions and help you select a system to suit your needs.
Inspecting Anchor Points
A competent person well-versed in identifying hazards and evaluating safety equipment must inspect permanent anchor points annually, though more frequent checks may be necessary. Anchor points and fall arrest systems often have unique inspection requirements. The user manual will contain manufacturer recommendations for inspections, including the ideal inspection schedule. Ensure proper documentation of these inspections by keeping the following information:
- The name of the competent person performing the inspection
- The date the inspection was completed
- The inspection’s findings, including any changes made to the system
Complete a visual inspection before attaching fall protection systems to your anchor points. Do not use the anchorage point if you see visible issues like corrosion, cracks, or other damage. Loose, weakened, or damaged fasteners directly affect the anchor point’s strength and stability.
If the anchorage point is in good condition, ensure you connect the shortest self-retracting lanyard that enables workers to perform their tasks. The retractable lanyard should not be attached to an anchor point below a worker’s shoulder height for their safety.
The excessive force exerted during a fall can weaken an anchorage point. If a worker falls, the manufacturer or an engineer with specialized fall protection training must test it to ensure it is still suitable for use.
If an inspection determines that an anchor point is damaged due to regular use or after a fall, remove it from service immediately.
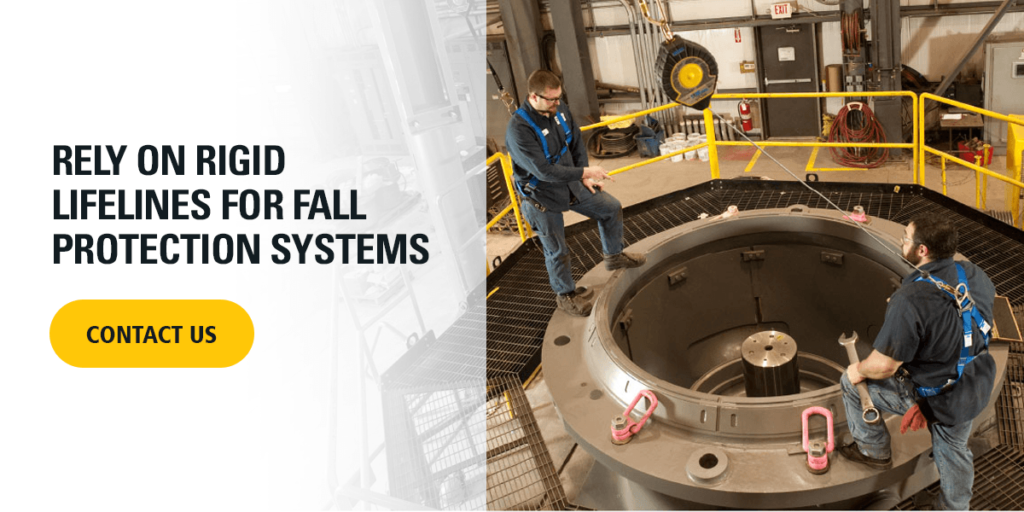
Rely on Rigid Lifelines for Fall Protection Systems
For over 20 years, Rigid Lifelines has provided reliable fall arrest systems that meet or exceed OSHA regulations and industry standards. We offer mobile and permanent fall protection systems, retractable lanyards, and harnesses to keep your crews as safe as possible. Contact us today to discover the right fall protection fit for your company!
Categories
Share this post
Let us help you
Contact us today to find the perfect product fit for your job
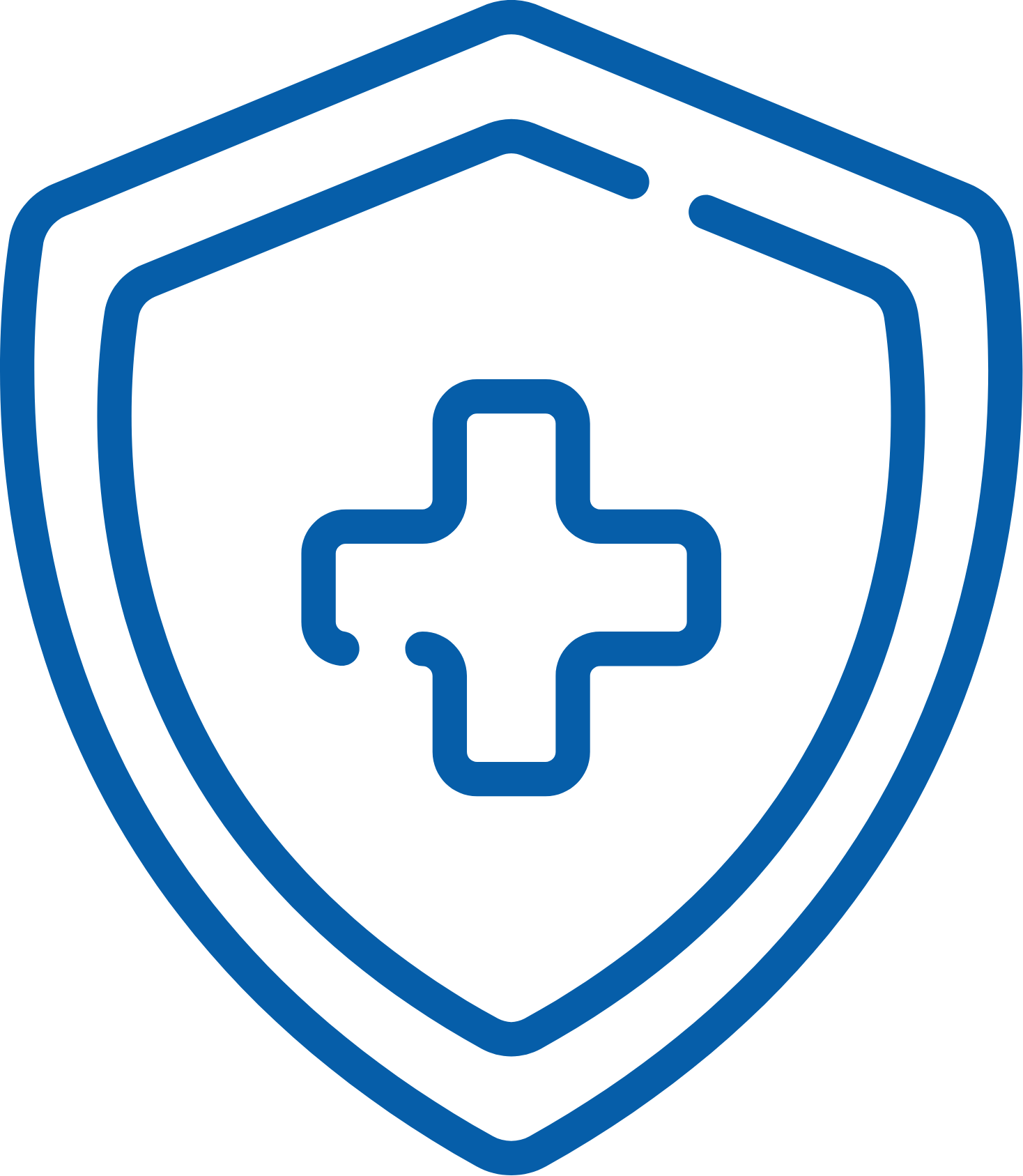