
The Evolution of Horizontal Fall Protection
April 15, 2025
The fall protection industry is evolving. In its earliest form, workers used hemp ropes to tie around their waists in the event of a fall. During the latter part of the 20th Century, advances in technology took the concept of a rope and put it overhead in the form of horizontal fall protection. Eventually the natural rope was replaced with wire rope. Now the industry is staging for the next step in the evolution of fall protection.
In recent years manufacturers of fall protection systems have been bringing new and innovative products to market. Twenty five years ago, one of these breakthrough safety innovations was the application of enclosed track (also called a rigid horizontal lifeline) to fall protection. These rigid horizontal lifelines dramatically reduce and sometimes completely eliminate the potential for injury compared to flexible rope horizontal lifelines. The untold story of flexible horizontal lifelines is that workers connect to these systems believing that if they fall, they will walk away unharmed. The truth is that while a wire rope or cable system may save a worker from death, they put the worker at risk, and can cause significant bodily injury due to the free fall distance it takes for a rope system to arrest a fall. These systems often make for a quick sale, however, OSHA requires that all flexible horizontal lifelines be designed by a Qualified Person. If you are using a flexible horizontal lifeline system that was not designed by a Qualified Person, it may not be safe or OSHA compliant.
Rigid Lifelines have more intrinsic benefits than rope systems.
Rigid horizontal lifelines differ from horizontal flexible lifelines in that they do not flex during a fall and do not generate any horizontal pull forces on the anchorages. This feature increases safety, reduces impact forces to the body, enables a better opportunity for self-rescue, simplifies component selection, and potentially eliminates fall injuries due to impacts to the body during the freefall.
There is a cost benefit to purchasing a Rigid Lifelines system.
Equipment maintenance is almost non-existent as there is no re-tensioning and no oiling or lubrication required. Users simply visually inspect before each use, and thoroughly inspect once a year. After a fall event, the system simply requires an inspection for defective parts by a competent person, and then the system can be placed back in service immediately. There is no need to red tag the system, shut down the whole operation, order new rope components, order rigging equipment, replace rope components, re-tension, and then recertify. On a Rigid Lifelines system, you simply inspect and go back to work. Rigid Lifelines systems also do not expire after a few years like some rope systems.
Rigid Lifelines simplify rescue planning.
Normally, a wire rope or cable system would need special lifting equipment or a nearby fire department to aid in the rescue of a person who’s fallen from height. Failure to rescue a fallen worker promptly can result in suspension trauma and can lead to permanent bodily injury or even death. When used properly, the average size worker who falls while using an overhead Rigid Lifelines system and SRL (self retracting lanyard) can simply steps back up onto the walkway or work platform. The perfect self-rescue! This can eliminate the need for special lifting equipment or a fire department. These benefits offer tremendous piece of mind for the safety engineer or Safety, Health & Environment (SH&E) professional, with regard to worker safety and rescue planning.
Rigid horizontal lifelines are not currently covered under any state, national, or international standards. This will change very soon as there is interest within the ANSI Z359.17 standards subcommittee to develop a dedicated standard to promote the safety of rigid horizontal lifelines. This new standard would address the unique requirements of rigid horizontal lifeline systems such as preventing lateral torsional buckling, accommodating dynamic lateral loading, structural analysis, specifying component compatibility, proper labeling, etc. This new standard would also assist the SH&E professional by removing some of the mystery and confusion involved when comparing and installing a rigid system, thereby increasing the safety for the fall arrest user.
If you are a SH&E professional considering the purchase of a horizontal fall protection solution, it’s time to consider a Rigid Lifelines system. You can benefit from the dramatically decreased anchorage forces, diminished fall distances, reduced swing hazards, lowered costs, simplified rescue planning, and the simple selection of a rigid lifeline system. Remember, fall protection is no longer just about satisfying OSHA. It’s about evolving to a new mindset where we not only protect our workers from injury and death, but also preserve their quality of life.
Originally posted 9/3/2010
Categories
Share this post
Let us help you
Contact us today to find the perfect product fit for your job
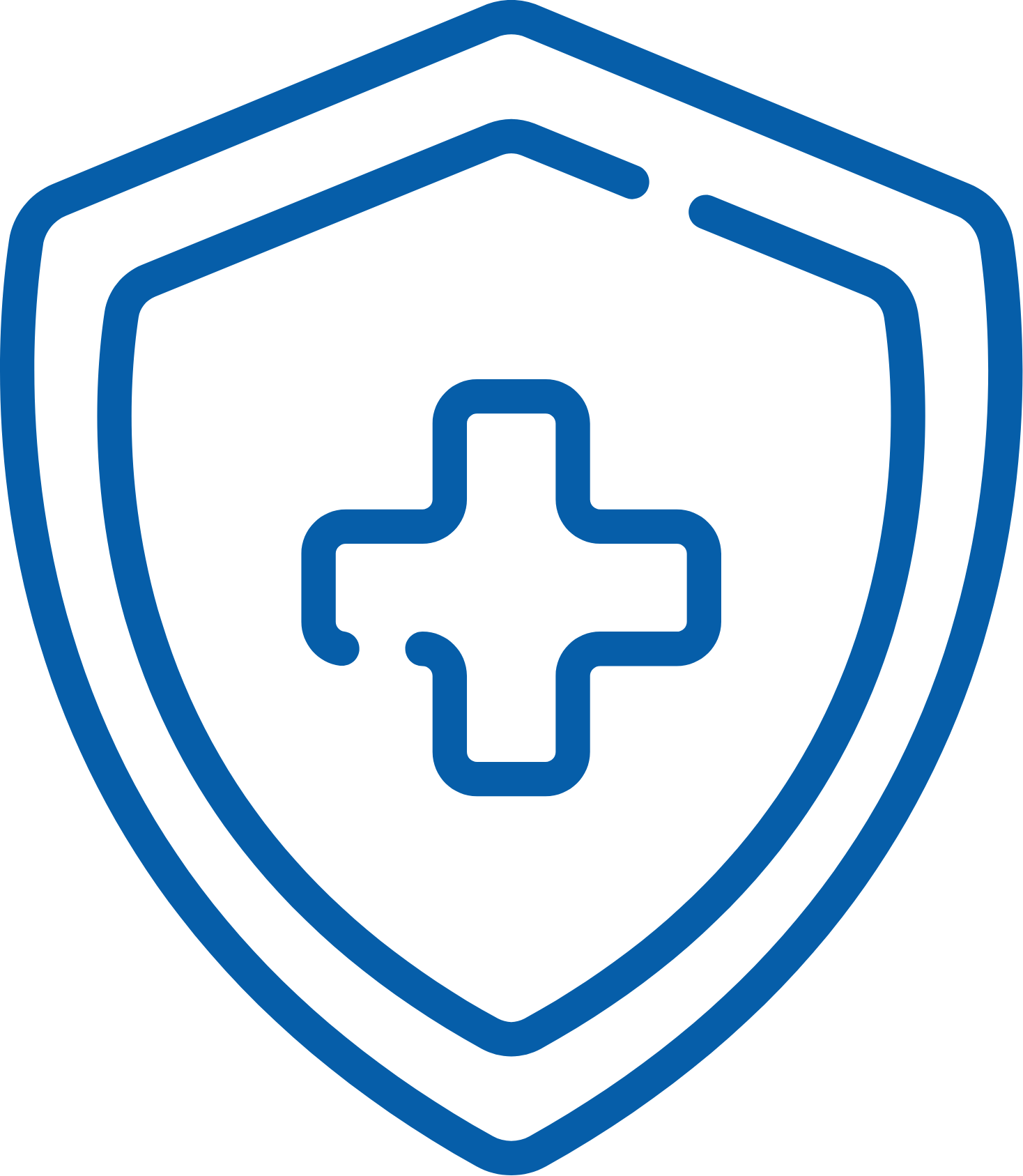