
Risk Assessment and Hazard Controls: Ensure Your Workers Are Safe from Unnecessary Risks
September 1, 2016
Risk assessment is the process of identifying hazards, analyzing or evaluating the risk associated with those hazards, and determining appropriate ways to eliminate or control them. Conducting a risk assessment requires a thorough look at your workplace or factory to identify situations, equipment, machinery, and processes that could potentially cause harm to workers or the facility as a whole. After hazards have been thoroughly identified, the next step is to evaluate the likelihood and severity of each hazard and decide which measures can be implemented to prevent or control hazardous risks effectively.
Risk assessments should be conducted by a team of competent people with a strong working knowledge of the application and workplace. It’s also a good idea to involve your staff and include supervisors and workers who are most familiar with the process and operation under review.
Five simple steps to identify hazards and assess workplace risk:
- Identify hazards
- Decide who is at risk and why
- Evaluate the risks and decide on precautions
- Record your findings and implement them
- Review the risk assessment and update when necessary
Step 1: Identify Hazards and Assess Workplace Risk
To start, consider how people could be injured in your workplace. When you work in the same facility every day, it is easy to overlook some hazards, so it can help to bring along a fresh set of eyes to help out with this step.
Next, walk around your workplace and determine what could reasonably be a hazard or cause harm to employees. Ask your employees what they think! They may notice hazards that aren’t immediately obvious to you. Check manufacturer’s instructions for chemicals and equipment; these instructions are very useful to outline potential hazards. Review your accident records because they can help to identify less obvious hazards. Consider long-term hazards to health AND safety. If you are a member of a trade association, contact them. Many associations will provide useful information to help you identify and control hazards.
In most facilities, workers are well aware of the risks associated with their job or work area, and necessary control measures are not difficult to apply. You may be surprised to find that your workers know which areas are most likely to induce a fall or slip, which loads are too heavy to move without an overhead lift system, and even which fire escape routes are blocked or locked.
Some hazard examples include:
- Blockages in aisles or electric cords running through workstations
- Exposure to harmful chemicals and substances
- Emergency door blocked by product or equipment
- Cracks in the wall
- At-height work areas that may lead to a fall
- Missing needle guard
- High noise levels
- And many more
Step 2: Decide Who Is at Risk and Why
In order to identify the most appropriate risk management methods, it’s important to identify who is at risk. Clearly identifying who is at risk does not involve necessarily listing every employee by name, but rather identifying which groups of people are at risk. Take the time to identify how these people might be harmed—or what type of injury may occur.
Keep in mind that certain groups of people may be at a higher risk for injury. For example:
- Workers with particular medical requirements—new or young workers, expectant mothers, people with disabilities, and workers with injuries
- Untrained workers without the skills necessary to complete a job safely
- Contractors, maintenance workers, cleaners, and visitors who aren’t in the workplace often
- The public, depending on the hazards identified
- Workers who do particularly hazardous tasks on a regular basis
Some at-risk examples include:
- Pregnant women using chemicals; the unborn child may be at risk of illness or disease
- Workers in areas with blocked exits and escape doors; not being able to escape in the event of a fire or other emergency
- Young, inexperienced, or untrained workers; unable to easily identify risks and/or avoid hazards
- Workers at height without appropriate fall protection or PPE
Step 3: Evaluate Each Risk and Decide on Precautions
After you’ve identified all of the hazards in your facility, you need to start thinking about how to prevent or eliminate them. Many regulations require you to do everything “reasonably practicable” to protect people from harm. The easiest way to protect workers is to compare and contrast what you’ve been doing to best industry practices. To start, look at what you’re already doing. For instance, note which controls you have in place and how work is organized. Next, compare your notes with best practice standards and decide if there’s more you could do to bring the work hazards up to standard.
Apply the principles below to control risks (in this order, if possible):
- Try a less risky option
- Prevent access to the hazard
- Organize work to reduce exposure to the hazard
- Issue personal protective equipment
- Provide welfare facilities (onsite clinic, eye washing station, etc.)
Some health and safety measures cost very little, like placing a mirror along a blind spot to prevent vehicle accidents. A mirror is a low-cost precaution that could easily help reduce or even eliminate risks. Failure to take simple precautions can cost a lot more money if an accident occurs. It’s always a good idea to involve workers to ensure that any potential controls you put into place will work in practice and will not introduce new hazards in the workplace.
Some examples include:
- Block off dangerous sections of the facility (like broilers)
- Switch to a less hazardous chemical
- Make sure escape routes aren’t blocked and emergency exit doors are unlocked
- Provide first aid boxes (including an eye washing station and burn treatment)
- Ensure washing stations are working effectively
- Provide proper clothing, footwear, gloves, goggles, etc.
- Put up barriers between pedestrians and traffic
Step 4: Record Your Findings and Implement Controls
Conducting your risk assessment and integrating the results into practice will—without a doubt—help to keep your workers and business safer. Recording the results of your risk assessment and sharing them with your staff can help encourage the implementation of safety controls. Keep it simple when writing down your results and implementing controls. For instance, “Welding fumes: local exhaust ventilation used and regularly checked,” or “Electrical Hazards: only one electrical plug to be used per electrical socket.” Your risk assessment should be thorough and reach conclusions that are safe and easy to implement.
You should be able to demonstrate the following:
- Proper checks were made
- You consulted workers to see who may be affected
- You dealt with all significant hazards, taking into account the number of people who may be at risk or involved
- Any precautions made should be reasonable, leaving the remaining risk very low
- You involved your staff or a representative throughout the process
- You must show documented evidence of this process
If, after conducting your risk assessment, you find that there are a lot of improvements that need to be made, don’t try to address everything at once. Instead, make a plan of action to deal with the most important hazards first and then continue to make improvements as time goes by for less risky hazards.
A good plan of action should include:
- Cheap or easy improvements that can be done quickly; this step may be a temporary solution in certain cases until more reliable controls can be implemented
- Implement long-term solutions to risks most likely to cause accidents or illness
- Implement long-term solutions to the risks with the worst potential consequences
- Train employees on any remaining risks and give them ways to control those risks on the job
- Conduct regular checks to ensure control measures remain in place
- Clearly assign responsibilities: who will lead what action and when
- Prioritizing and tackling the most important tasks first. As you complete each action, check it off your plan
Step 5: Review Your Risk Assessment Regularly and Update When Necessary
Your workplace will change over time! At some point, you will inevitably bring in new equipment, machinery, substances, and even processes that could lead to new hazards. For this reason, it’s very important to review your risks on a regular basis. Reviews may be monthly, or even bi-yearly in some instances. It’s up to you to understand your risks and decide how often this process should be repeated. But, WRAP (The Worldwide Responsible Accredited Production Organization) recommends conducting a thorough risk assessment AT LEAST once a year or more to ensure you are still improving your hazard controls and reducing workplace risk and injury.
WRAP recommends the following:
- Look at your risk assessment again.
- Have there been any changes?
- Are there improvements you still need to make?
- Have your workers spotted a new problem?
- Have you learned anything from accidents or near misses?
Make sure your risk assessment is always up to date. It can be annoying to review your risk assessment on a regular basis, and it’s all to easy to forget to do it. That is, until something has gone wrong and it’s too late. It’s not a bad idea to set a review date for your ongoing risk assessments. Write them down and note them in your calendar as an annual event.
But, you don’t always have to wait for your review to pop up in your calendar to conduct another risk assessment! Throughout the year, note any significant change made to your facility. Check your risk assessment and amend it wherever necessary. Best practice is to begin thinking about risk assessment while you’re planning changes to your facility. This practice gives you more flexibility and helps you to continue your risk assessments as things change over time.
WRAP requires facilities to conduct health and safety risk assessments. Taking these steps is an essential part of your internal monitoring process. To review these requirements, please refer to Principle 1.4, 8.3 and 8.4 in the Production Facility Self-Assessment document, which can be found on here on WRAP’s website
Categories
Share this post
Let us help you
Contact us today to find the perfect product fit for your job
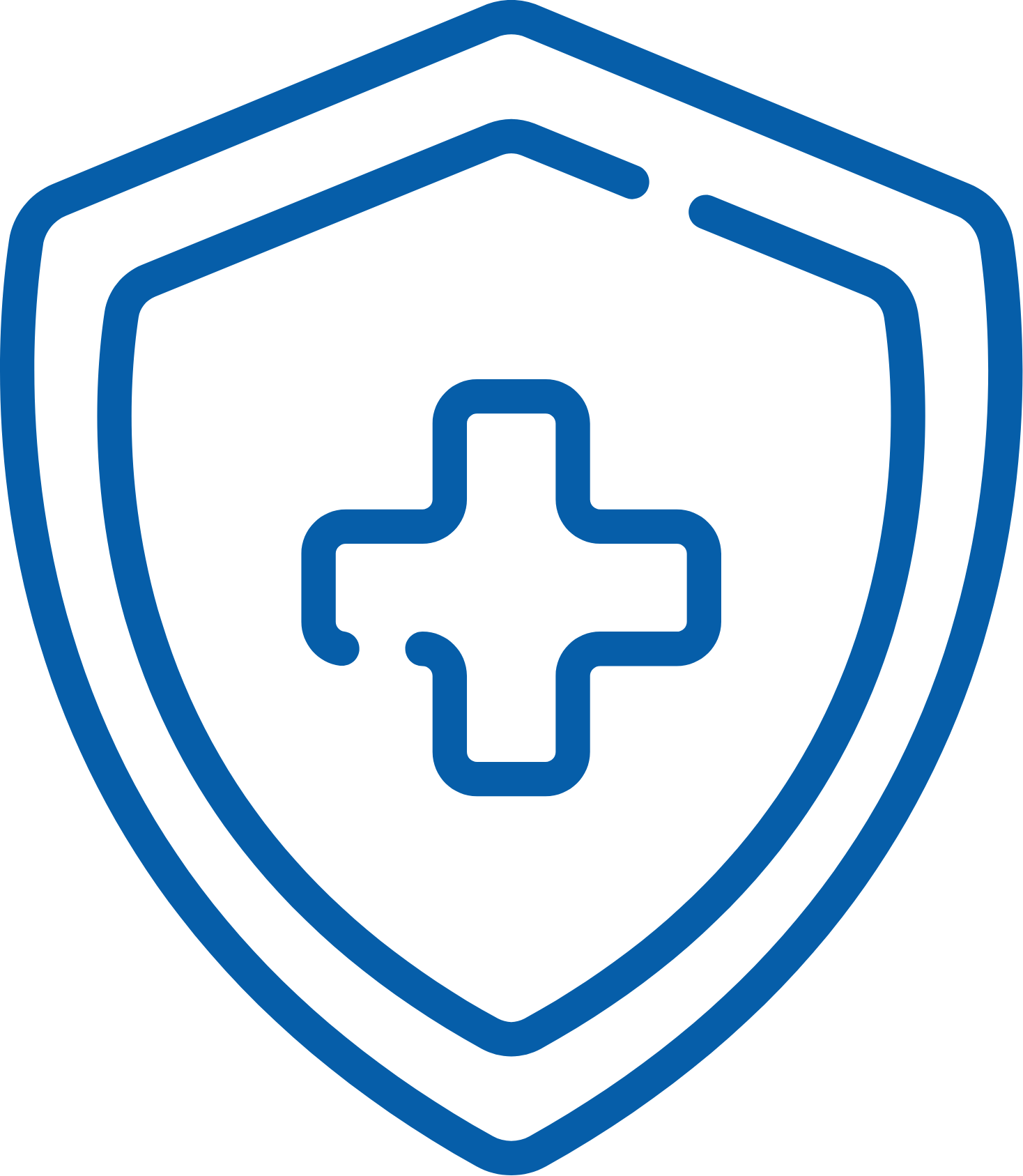