
Harness Materials and Degradation
May 31, 2013
Full body harnesses have a very significant role in a fall protection system. Although every major part of a fall protection system is important, the full body harness is the part that is closest to the worker and literally connects the worker to the rest of the fall protection system. The harness is a very influential part of fall protection because it is the part of the system that the worker needs to wear and that will ultimately support their weight in the event of a fall. Those two functions mean that the harness needs to be both comfortable and strong.
Web strap technology has been rapidly expanding over the last decade or so. And at this point, there are four different types of web strap material that are being used for full body harnesses designed for applications in fall protection. Nylon and polyester are the two most common materials for full body harnesses. But, Kevlar®, Nomex®, and Dyneema® are materials that are becoming more popular in full body harness manufacturing. Each material has specific benefits and deficits that should be understood in order to ensure that you make the right choice when it comes to selecting the material of a full body harness. The material is important because certain materials are more durable and useful for certain applications.
Nylon was originally a very popular material for full body harnesses in the early stages of fall protection technology. The nice thing about nylon is that it is soft and flexible, with relatively high break strength. Most nylon materials have break strength between 1,400 and 5,500 pounds. The overall break strength of the harness is established by the thickness of the material. Since nylon is more of a soft material, it does have the ability to stretch when enough weight is added to it. The ability to stretch may be desirable for some applications and completely undesirable for others. Please consider harness stretch and how it may impact your fall protection situation. A negative element of nylon is the fact that it absorbs water rapidly and can get moldy. Wet nylon is weaker than dry nylon, so the presence of moisture or the growth of mold can weaken the strength of a nylon harness.
Polyester is widely used by many harness manufacturers. The popularity of polyester stems from the fact that it is a much more durable material than nylon. Polyester harnesses have a higher resistance to abrasion. Since polyester is a more rigid material, it does not stretch the way that nylon does. It also resists water absorption, which reduces the likelihood of material degradation from mold growth. The average break strength of polyester is between 1,500 pounds and 10,000 pounds.
Kevlar®, Nomex®, and Dyneema® are three of the newest materials that are being used in full body harness manufacturing. Each material has a specific function in industrial fall protection. Kevlar and Nomex are perfect for welding flash applications because they are flame retardant with a high heat resistance. Meanwhile, Dyneema has excellent abrasion and cut-resistance. If a worker needs to perform a task at height where they either need to use welding tools or they need to be in an abrasive area, it’s a wise move to consider a harness that is made out of these materials.
There are some specialized environments where a worker who is exposed to heights may need to consider using a harness that is designed for a specific application. Consideration for environmental factors is an important part of the planning process that safety managers should keep in mind. Factors that could influence the effectiveness of the full body harness are the amount of dirt generated by the work area, exposure to abrasive chemicals (like battery acids), and exposure to ultraviolet rays. Some materials are better suited to certain environments. If you have an unusual environmental exposure, make sure to consider that as you select your harness.
A NOTE ON ULTRAVIOLET EXPOSURE: Both nylon and polyester have different reactions when exposed to ultraviolet rays. Robert Golz serves on the ANSI Z359 Fall Protection Code committee and has had 42 years of experience in the web strap industry. During his time with ANSI, Golz developed a presentation that discussed the different factors that can influence full body harness web strap degradation. A portion of his presentation included a series of tests that were conducted by a fall protection company in Florida. We’ll go into the other details about the Florida tests and other elements of Bob’s presentation in another blog. For now, we’re just going to discuss the effects of ultraviolet exposure on nylon and polyester.
The goal of the ultraviolet testing was to determine how much the materials of the full body harness would be weakened by regular exposure to the ultraviolet rays in sunlight. Essentially, harnesses that were made of nylon and polyester were exposed to direct sunlight (under glass to keep them dry) for 8 hours a day for varying lengths of time and then they were put through different tensile strength tests. Initially, the nylon retained 90% of its original breaking strength and the polyester retained 80% of its original break strength. After 4 months of exposure, the nylon retained 69% of its original break strength and the polyester retained 68% of its original break strength. Both fabrics maintained an even level of original break strength between 5 and 7 months. And all tests conducted after a year, showed that the polyester retained a higher percentage of the original break strength than the nylon.
Now, you have a better idea of what types of harness materials are best suited for certain types of working applications. In next week’s blog, we will discuss more information about the materials that comprise full body harnesses and the future of harness technology. Until the next time, stay safe up there!
Categories
Share this post
Let us help you
Contact us today to find the perfect product fit for your job
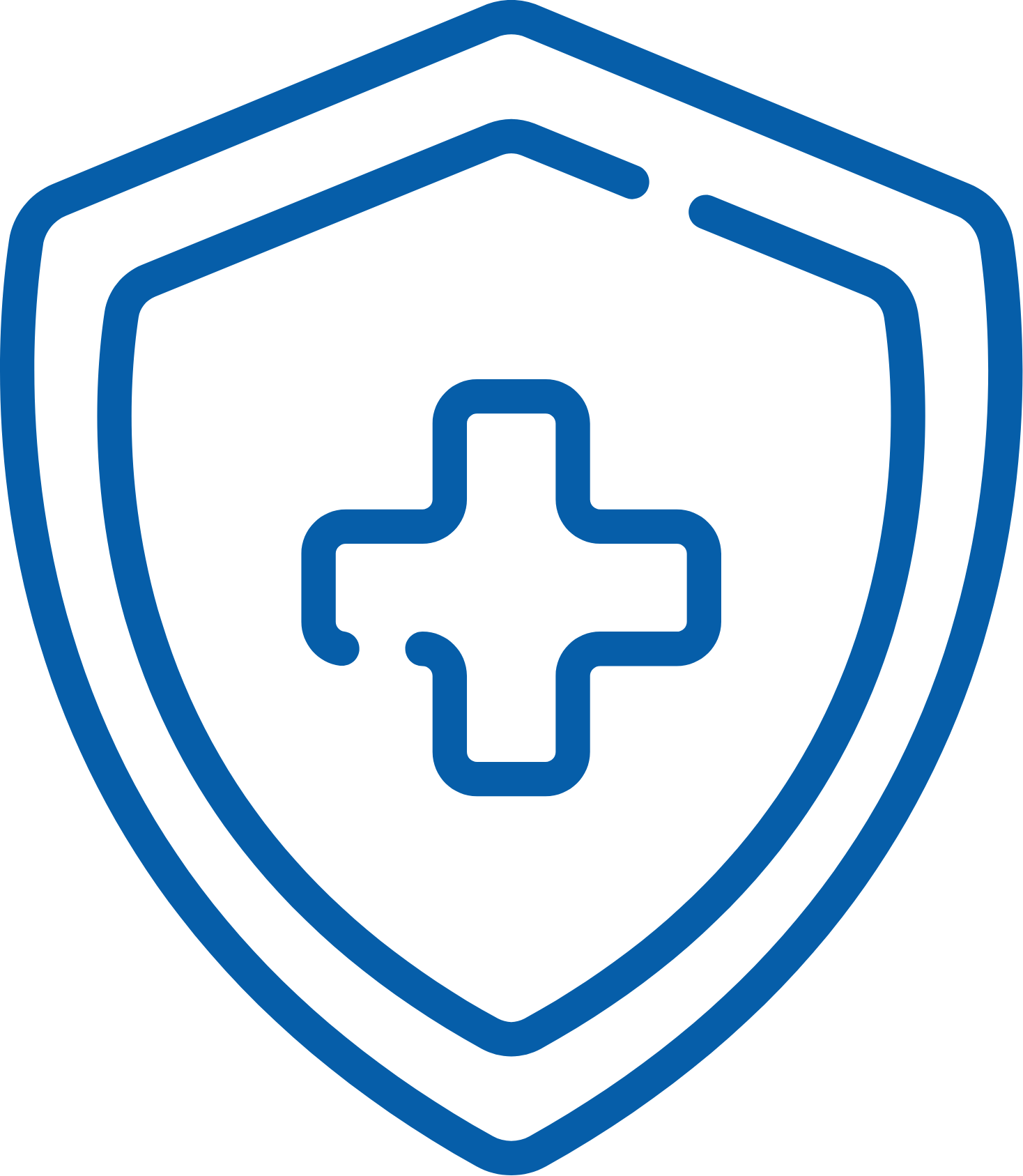