
Flexible Lifelines vs. Rigid Lifelines
May 17, 2013
Horizontal lifeline fall protection is an important system to have in any facility or situation where people must work at height. But deciding which type of fall protection system is best for your particular application can be a difficult choice. For this reason, it’s important to understand the advantages and disadvantages of both flexible lifeline and rigid lifeline styles of horizontal fall protection systems.
Although many of the components are the same in each system, those similar parts are applied in different ways and in different applications. When you cut through the rhetoric, the bottom line is that flexible lifelines (as the name implies) will deflect—sometimes significantly. Meanwhile, a rigid lifeline (once again, applicable name) does not deflect. Generally speaking, the entire function of a fall arrest system is to stop the fall. But the amount of deflection that the system allows will determine the amount of fall distance that a worker experiences after a fall. And, as our head of R&D likes to say, “The farther you fall, the greater your chances of serious injury.”
The advantage of a flexible lifeline type of fall protection system is that it is most effective when workers temporarily need fall protection, commonly found in the construction industry. A flexible lifeline is attached to the anchorage structure via an anchorage connector. That anchorage connector attaches to an energy absorber and a tensioner. And the tensioner holds the actual cable that makes up the flexible lifeline where the worker connects to the system. The tensioner determines how much force will be exerted on the energy absorber in the event of a fall. Meanwhile, the energy absorber is designed to reduce the maximum forces of the fall on the anchorage structure. Please note that these types of energy absorbers usually limit the maximum dynamic load on the building to 2,500 lbs.
The horizontal lifeline energy absorber (or HLLEA) on flexible lifelines is designed to reduce the stress exerted on the anchorage structure. These devices are different from personal energy absorbers which are used to connect the worker’s harness to the lifeline system. And remember, most personal energy absorbers are set to 900lbs average arresting force. There is a huge difference between the arresting forces of a lifeline energy absorber and a personal energy absorber. Please make sure that you are using the right kind of energy absorber for your circumstance.
The HLLEA limits forces typically by either using a retractable cable braking device or a rolled, flat piece of metal that comes undone when weight is added to it. Remember, that this process will increase the fall distance for the worker connected to the line during fall arrest. Since the cable bends/deflects in the direction of the weight, the force on the cable becomes multiplied. The force on the cable will cause more force to be exerted on the anchorage connector and energy absorbing devices. Lateral forces contribute to the deflection and the amount of force exerted on the anchorage structure. In turn, this deflection energy will allow the worker to fall farther, thereby increasing the chance of injury.
On a rigid lifeline fall protection system, the track of the system is attached directly to the anchorage structure, typically with hanger clamps. Then, the worker connects to the track by hooking their personal fall protection to the trolley. In a rigid lifeline application, the force of the fall is always going to be primarily vertical against the anchorage structure. The combination of vertical force, no lifeline deflection, and almost instant arrest with an SRL device means minimal forces will be exerted on the fallen worker.
The rigid horizontal fall protection system is useful for permanent installations where workers are regularly accessing areas of height in order to do their job. However, the advances in portable fall protection systems are allowing rigid lifeline systems to be available in new locations. The proper application of rigid horizontal fall protection systems allows for primarily downward forces to be exerted in the event of a fall. This reduces fall distance for the worker and thusly reduces the amount of injury for a worker. Since the force is primarily vertical, the actual anchorage support structure will most likely not need reinforcement because there are NO lateral forces occurring. And, since there is no permanent deformation of any of the components of the fall arrest system, there is minimal inspection and maintenance that needs to occur in order to return the system to service after a fall.
There are many equations that are used in the fall protection industry, but one of the most important equations is a relatively simple one:
Force X Distance = Energy
In order to reduce the chance of injury to the worker attached to the system, it is always the goal of the fall protection engineer to find a way to keep the energy exerted on the worker to a minimum by reducing the fall distance created by the fall arrest system.
Thank you for reading and stay safe up there!
Hannah Addison
Categories
Share this post
Let us help you
Contact us today to find the perfect product fit for your job
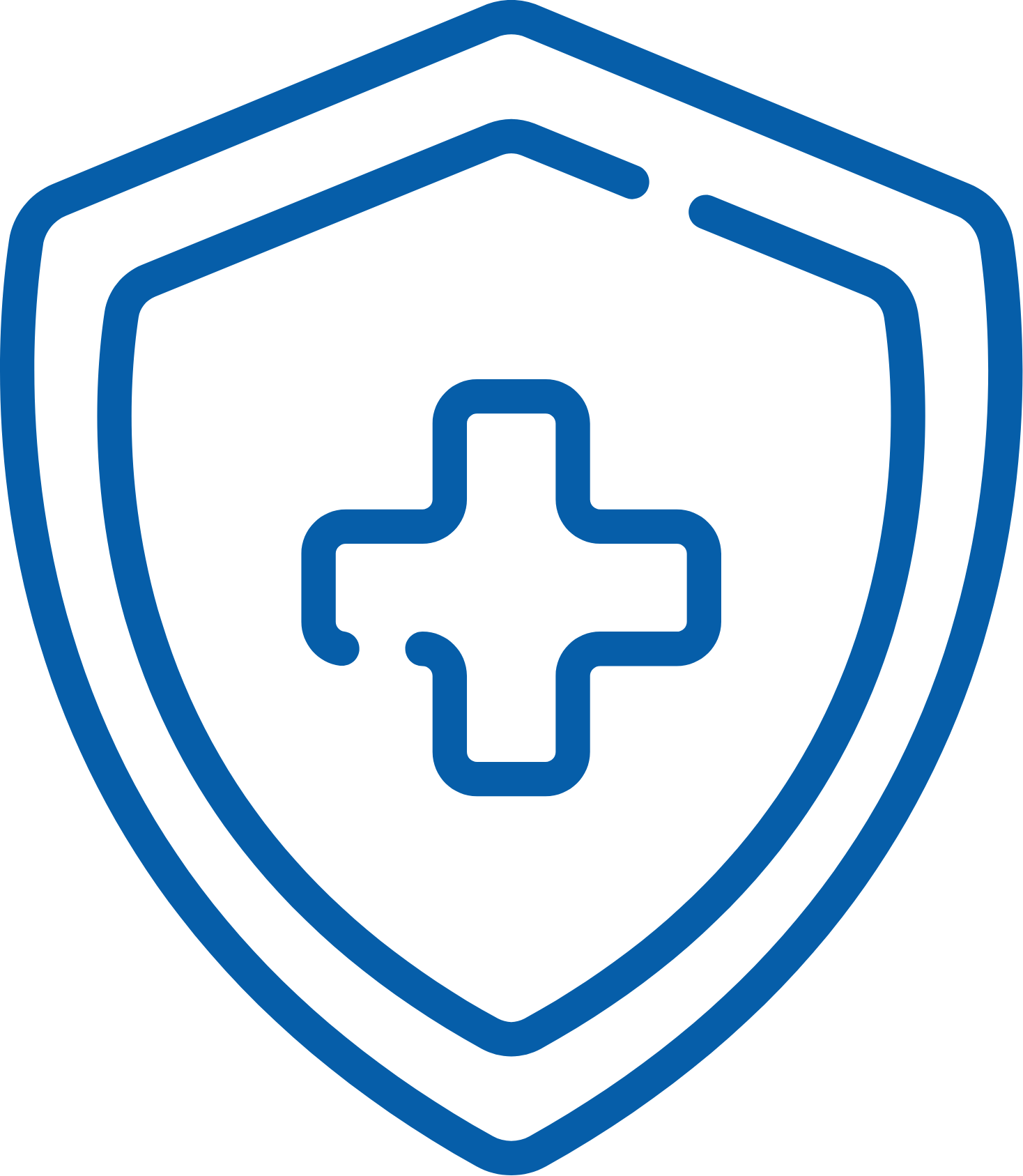