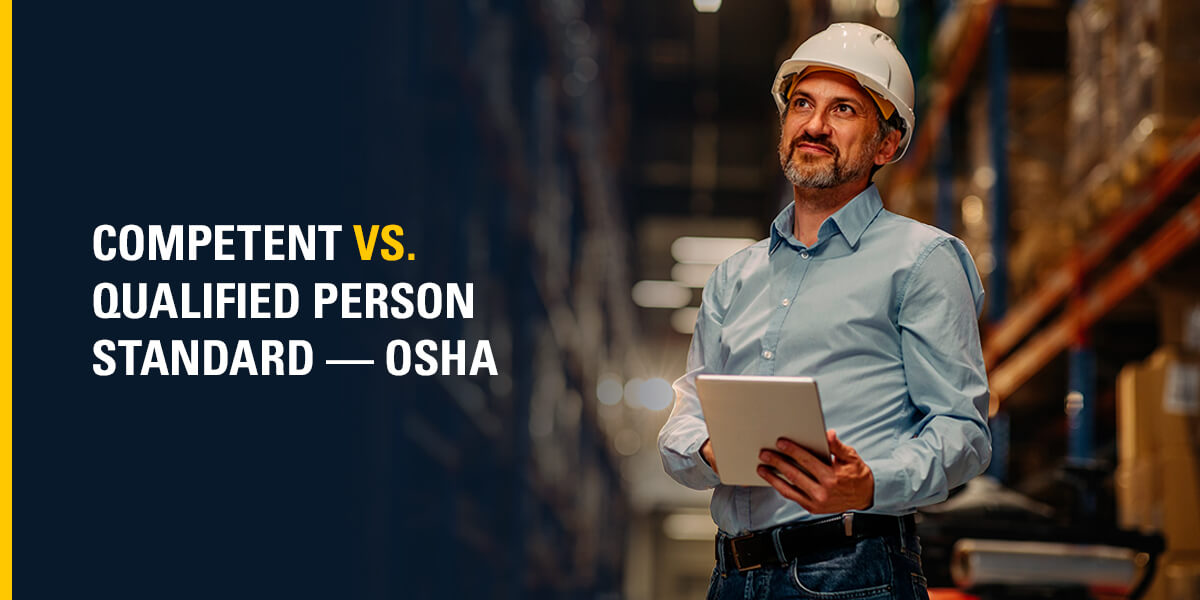
Competent vs. Qualified Person Standard — OSHA
July 8, 2022
Properly identifying hazards in the workplace is a critical aspect of risk reduction and can, quite literally, make the difference between life and death. Meeting standards from the Occupational Safety and Health Administration (OSHA) and selecting a competent person are necessary for protecting workers. It’s the employer’s responsibility to choose the right person to identify hazards and conduct equipment inspections and safety assessments.
But who is a competent person? Who can be considered qualified? Understanding the OSHA definitions for a competent person vs. a qualified person is necessary for complying with regulations and keeping your employees safe.
Competent Person Definition
Competency is based upon experience and knowledge of safety practices. OSHA defines a competent person as “one who is capable of identifying existing and predictable hazards in the surroundings or working conditions which are unsanitary, hazardous, or dangerous to employees, and who has authorization to take prompt corrective measures to eliminate them.” Although this definition is taken from the standard for the construction industry, it is used as the universal definition throughout OSHA standards.
Many employees may have the ability to recognize hazards. Employees can also take classes to learn more about safety hazards in their line of work. However, an employee can only be considered an OSHA “competent person” if they also have the authority to correct the issue or stop the work until it can be corrected. The competent person does not have to take any classes or have recognized training, but must have demonstrated the ability to fulfill the requirements.
It’s the employer’s responsibility, not OSHA or the state, to select competent persons and ensure they meet all the requirements. During OSHA inspections, they may ask who the competent person is supposed to be. They may question the person and see if other employees know who the competent person is.
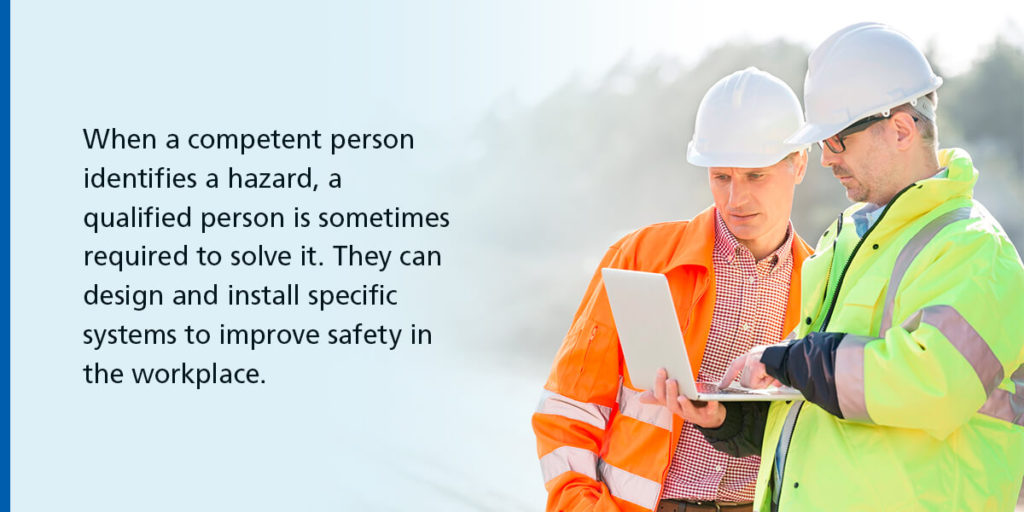
Qualified Person Definition
OSHA defines a qualified person as “one who, by possession of a recognized degree, certificate, or professional standing, or who by extensive knowledge, training, and experience, has successfully demonstrated [their] ability to solve or resolve problems relating to the subject matter, the work, or the project.” Therefore, to be considered a qualified person, one must have professional training and recognition for successfully completing it.
When a competent person identifies a hazard, a qualified person is sometimes required to solve it. They can design and install specific systems to improve safety in the workplace. However, a qualified person may not have the authority to stop work.
In some cases, the competent person may also be the qualified person; they just have to meet the requirements of both roles. For example, the person designated as the competent person could also have the degree necessary to fulfill the duties of a qualified person.
What Is the Difference Between a Qualified and Competent Person?
When you’re looking at these definitions, it can be difficult to distinguish a qualified vs. a competent person. Both people need to be able to identify and solve problems in their workplace. However, there are a few differences.
Competent Person
A competent person focuses on hazards. They have demonstrated their ability to identify existing and potential hazards in the workplace. They know which conditions can be considered unsanitary or dangerous to employees. While a qualified person may have more technical expertise and also be able to recognize hazards, a competent person has the authority to correct or eliminate them.
Overall, a competent person has:
- Expertise in hazard recognition.
- Authority to correct hazards.
- Demonstrated their ability.
Qualified Person
A qualified person has certified ability in a specific aspect of the work, which may or may not be related to the safety of the workplace. A qualified person improves safety by designing or installing systems that solve problems or remove potential hazards. Another difference is that, in many industries, a competent person is required to be onsite, while a qualified person is not.
A qualified person has:
- Technical expertise in the area.
- A certification, degree, or other professional recognition.
Industry Examples
On a construction job site, a competent person and a qualified person serve different purposes. A competent person could identify a falling hazard and stop work. A qualified person would have the technical expertise to design or install fall protection systems to be used. Then, the competent person could allow the work to be resumed.
In general industry, suppose the most experienced and knowledgeable team member notices a potential hazard. If they have to call someone else to stop work or make a change, that person is not the competent person, even if they are viewed as the expert, since they don’t have the authority to stop or change the work. If they are a qualified person, they can implement safety systems after the competent person has stopped work and approved changes.
OSHA and ANSI Uses
When it comes to fall protection, the American National Standards Institute (ANSI) also has a definition for a competent person and another for a qualified person.
ANSI defines a competent person as “an individual designated by the employer to be responsible for the immediate supervision, implementation, and monitoring of the employer’s managed fall protection program who, through training and knowledge, is capable of identifying, evaluating, and addressing existing and potential fall hazards, and who has the employer’s authority to take prompt, corrective action with regards to such hazards.”
ANSI defines a qualified person as “a person with a recognized degree or professional certificate and with extensive knowledge, training, and experience in the fall protection and rescue field who is capable of designing, analyzing, evaluating, and specifying fall protection and rescue systems to the extent required by this standard.”
OSHA requires fall protection for distances greater than 4 feet in general industry and 6 feet in the construction industry. OSHA’s General Duty Clause requires employers to provide a work environment free from known hazards that can cause death or serious injury. Industry-specific OSHA standards — including those for general industry, shipyards, longshoring, and construction — can be found on OSHA’s website.
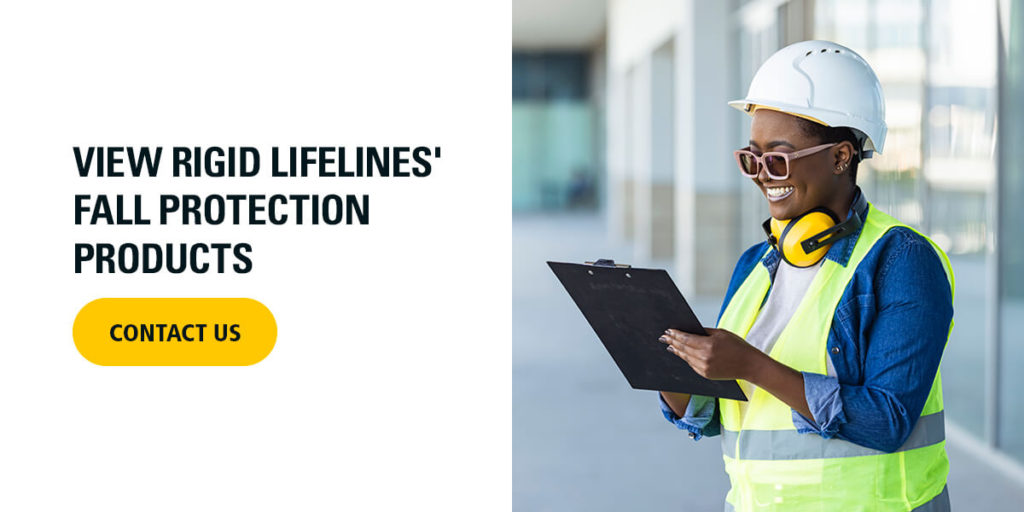
View Our Fall Protection Products
Rigid Lifelines offers a wide range of permanent and mobile fall protection systems for workers in indoor and outdoor environments. All our rigid rail systems comply with OSHA and ANSI regulations, which allows us to help you reduce workplace risks and keep improve worker safety. We stay up to date on fall protection codes and ensure each of our custom fall protection systems meets those guidelines.
Use our system selector to find the best product for you and your employees. We offer both fall arrest and fall restraint systems. Find a rep or contact us to learn more about providing fall protection for your employees.
Categories
Share this post
Let us help you
Contact us today to find the perfect product fit for your job
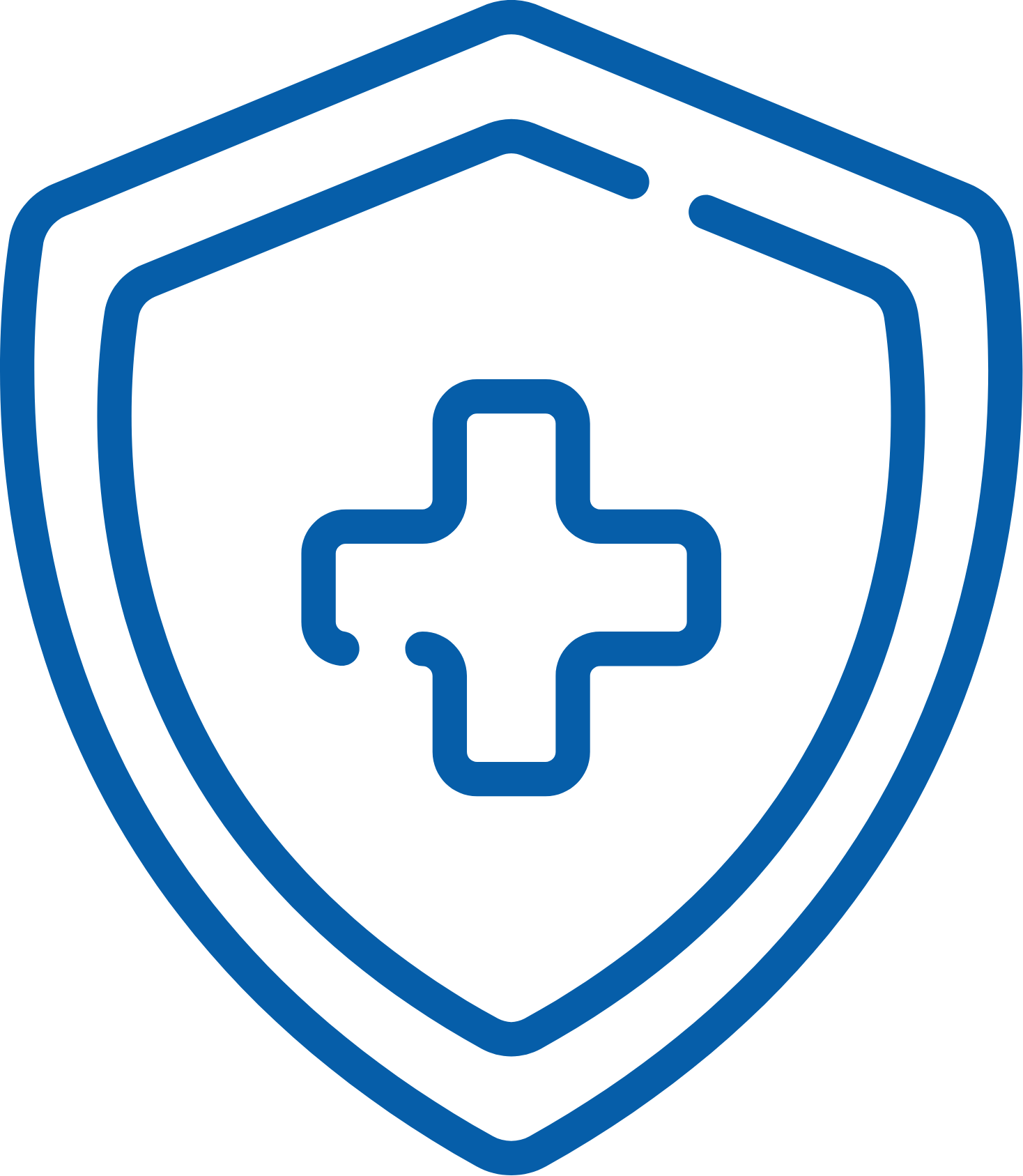