
An Effective Contractor Safety Program
October 23, 2015
Many large jobs in the construction industry involve employing contractors to do specialized assignments around the jobsite. These contractors are exposed to general and industry-specific hazards based on the type of work they perform. Unfortunately, if these contractors are injured or injure others, the employing company can be held accountable. For that reason, it is important to keep contractors safe. An effective contractor safety program can help keep contractors safe on the jobsite by implementing safe practices throughout the contractor hiring process.
An effective contractor safety program begins with a prequalification process. During the prequalification process, employing companies should require the contractors to prove that they have appropriate worker compensation and general liability insurance with adequate coverage. The prequalification process should also require the contractors to prove that they have an effective safety program by requiring them to submit all applicable written safety policies for review. An employing company should also require the contractor to submit prior incident rate data including employee training documentation and the contractor’s experience modification rate (EMR). EMR is a number used by insurance companies to gauge both past cost of injuries and future chances of risk. After the employing company reviews all of the submitted information, it will approve or reject the contractor. If the contractor is approved, the employing company can move to the next step of the contractor safety program—communication hazards.
The employing company must communicate each hazard that the contractor might encounter on the jobsite. Hazards might include exposure to hazardous chemicals, working at height, vehicle traffic, or electrical hazards. Employing companies often use a hazard analysis checklist to communicate the hazards. The checklist should identify the specific company policies that will apply to the jobsite and the steps and hazards involved in each phase of the project. After the hazards have been identified, they should be addressed by using the National Institute for Occupational Safety and Health’s (NIOSH) hierarchy of controls. Addressing hazards correctly might include elimination, substitution, engineering controls, administrative controls, or personal protective equipment. An employing company should use a new checklist for each project because each jobsite often presents different hazards. Both the employing company and the contracting company should complete the hazard analysis checklist to ensure that both companies understand the dangers involved with the specific jobsite. The next step in an effective contractor safety program is enforcing the contractor safety program.
Contractors must understand that violating the policies and procedures presented in the contractor safety program will not be tolerated. If contractors violate any policy in the safety program, they must be held responsible or potentially terminated. Enforcing the contractor safety program will prevent injuries and ensure that the project is completed safely and efficiently. By implementing an effective contractor safety program, companies can help keep contractors safe and ensure that they hire the right contracting company for the job.
Categories
Share this post
Let us help you
Contact us today to find the perfect product fit for your job
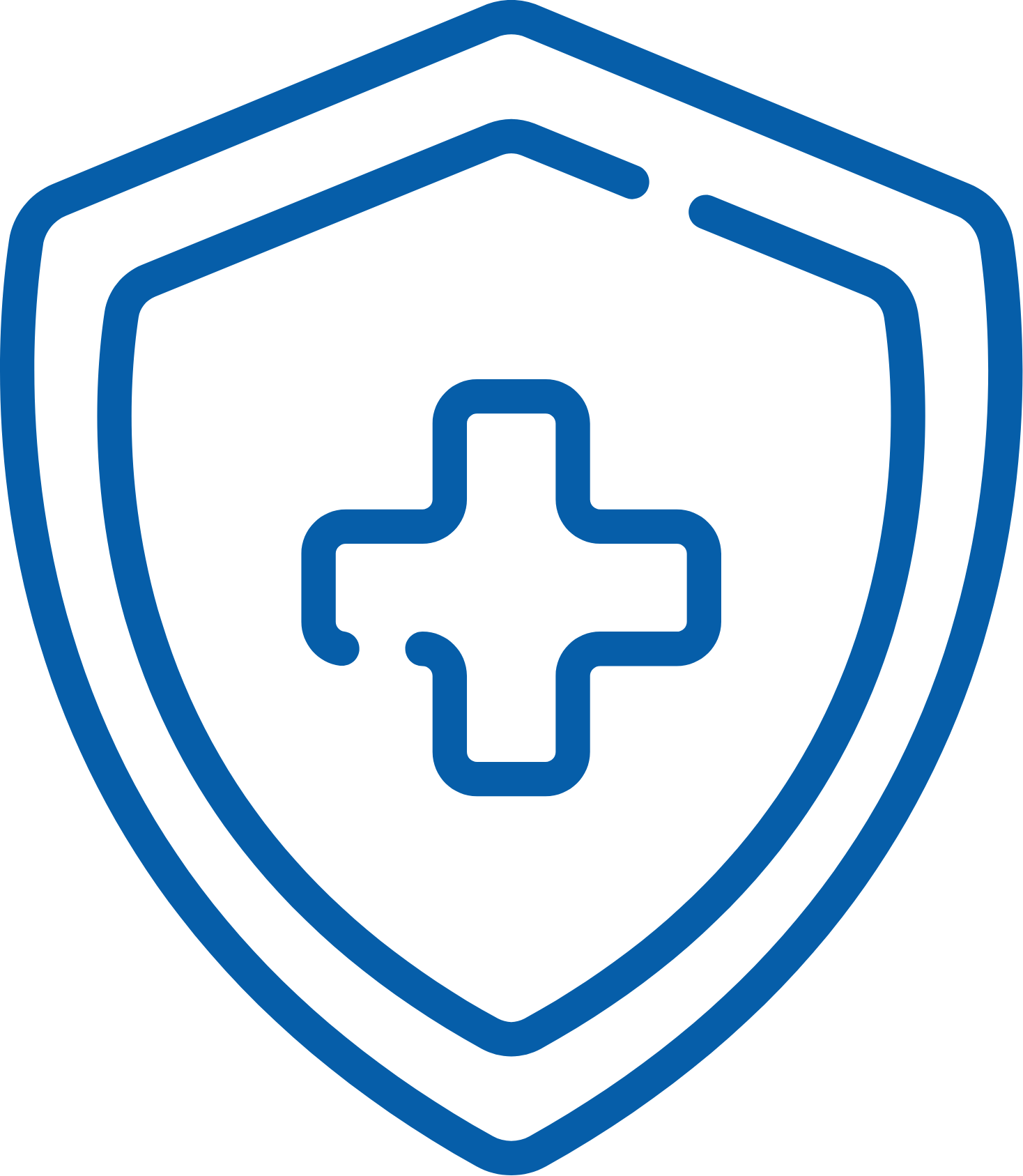