
Inspecting Your Full Body Harness
December 9, 2024
Inspecting Your Full Body Harness
When a person is using a fall protection system, every component of the system makes an important contribution to the safety of the user. Even though each part of a fall arrest system is important, the device that is most often complained about is the full body harness.
Any fall protection system is only as effective as its components, each of which must be inspected and maintained to ensure integrity and proper operation. Here we’ll briefly review the various parts of the full-body safety harness, and highlight the basics of harness inspection.
Before each harness use, you should follow these inspection points:
General
It is essential for workers to inspect their harnesses before each use. Workers need to check for any tag or label noting the harness’s last inspection date and its condition at that time. A worker should never attempt to don a harness that has failed inspection. Failed equipment should be disposed of in a way that avoids accidental use. Also check the manufacturing or “in-use” date to ensure that the harness has not exceeded its working life of five years.
- Visually inspect the harness to make sure that the fall indicator warning label is not showing. If the fall indicator warning is showing, IMMEDIATELY remove the harness from service.
- Inspect the harness for label presence and legibility.
- If the harness shows any signs of noticeable wear or damage, defect, inadequate maintenance, or unsafe condition, it must be removed from service immediately.
- If a harness has arrested a fall, it should be removed from service and replaced with a new one.
- Sewn terminations must be secure, complete, and not visibly damaged.
- All markings must be legible and attached to the product.
- All hardware must be free of cracks, sharp edges, deformation, corrosion, or any evidence of defect.
Webbing
The webbing, or main body of the harness, is typically nylon or polyester and can be inspected first by holding the harness up and ensuring that the webbing hangs evenly. Then, the webbing can be inspected in segments of approximately 6″ to 8″ by bending each segment into an inverted “U” shape and checking for any signs of rips, fraying, fatigue (or thinning), abrasions, cuts, broken fibers, or chemical or corrosive damage. Fading of webbing color can indicate UV wear and should also be noted. Harnesses designed with tattle tale webbing will expose bright red or other colored fibers to alert the user to significant wear. Follow manufacturer’s guidelines for replacement of any damaged portion.
- Inspect webbing by bending 6 to 8 inches of the material into an upside-down U-shape and checking the material for tears, cuts, fraying, abrasion, discoloration, burns, holes, mold, pulled/broken stitches, or other signs of wear/damage.
- Adjust keepers, buckles, padding, and D-Ring to inspect webbing hidden by each component.
- Webbing should not have additional punched holes.
D-Rings
As with any hardware that endures stress in the course of its duties, D-rings should be inspected carefully for any bending, distortion, rust, corrosion, cracks, nicks, burns, deep scratches or other signs of fatigue. The general rule for rust damage is that no more than 15% should be affected. As a quick test, if one can rub the rust between thumb and forefinger, the ring has failed inspection. Also check D-rings for any sharp edges that could damage webbing or injure workers. D-rings should move freely and pivot without creating tension.
Grommets & Belts
Like D-rings, grommets are subject to wear, damage, and fatigue. Check for any distortions, sharp edges, nicks, cuts, improper closures, chemical damage, or corrosion. Grommets should be snug, so check for looseness. Also be sure that grommets haven’t created unwanted holes in the harness webbing.
If the harness has tongue buckles, the tongue buckle/grommet tongues should be free of distortion in shape and motion. They should overlap the buckle frame and move freely back and forth in their socket. The roller should turn freely on the frame. Inspect buckle for loose, distorted, or broken grommets.
Buckles
Buckles should be checked for any distortions or sharp edges. Check the attachment points of the center bar and that the roller moves freely. Also check rivets for signs of bends, fatigue, or corrosion. Slots through which the webbing passes should be straight and free of sharp edges. Any portion of the webbing that contacts the buckle should be checked for additional signs of fatigue, as these are more likely to occur at such friction points. For tongue buckles, tongues should overlap the buckle frames.
- Check all buckles for damage, distortion, cracks, breaks, and rough or sharp edges. Inspect for any unusual wear, frayed or cut fibers, or broken stitching of the buckle attachments. Make sure buckles are properly engaged.
- The outer bars and center bars on friction and slotted mating buckles must be straight.
- Ensure that the quick-connect buckle dual tab release mechanism is free of debris and engages properly. Double-check the buckle locking mechanism by tugging on both halves of the buckle to make sure it is firmly connected and will not disengage.
Please note: These inspection points are meant as a minimum guideline and are not all of the potential inspection points that may be required for your particular situation. PLEASE FOLLOW ALL INSPECTION PROTOCOLS AS OUTLINED IN YOUR PERSONAL FALL PROTECTION TRAINING COURSE.
The best way to ensure that any fall protection device performs properly and reliably is through proper inspection and maintenance. Safety managers should take the time to educate workers on proper harness inspection and should reinforce frequent inspection with the use of tools like inspection log books. When it comes to safety it pays to be diligent.
Categories
Share this post
Let us help you
Contact us today to find the perfect product fit for your job
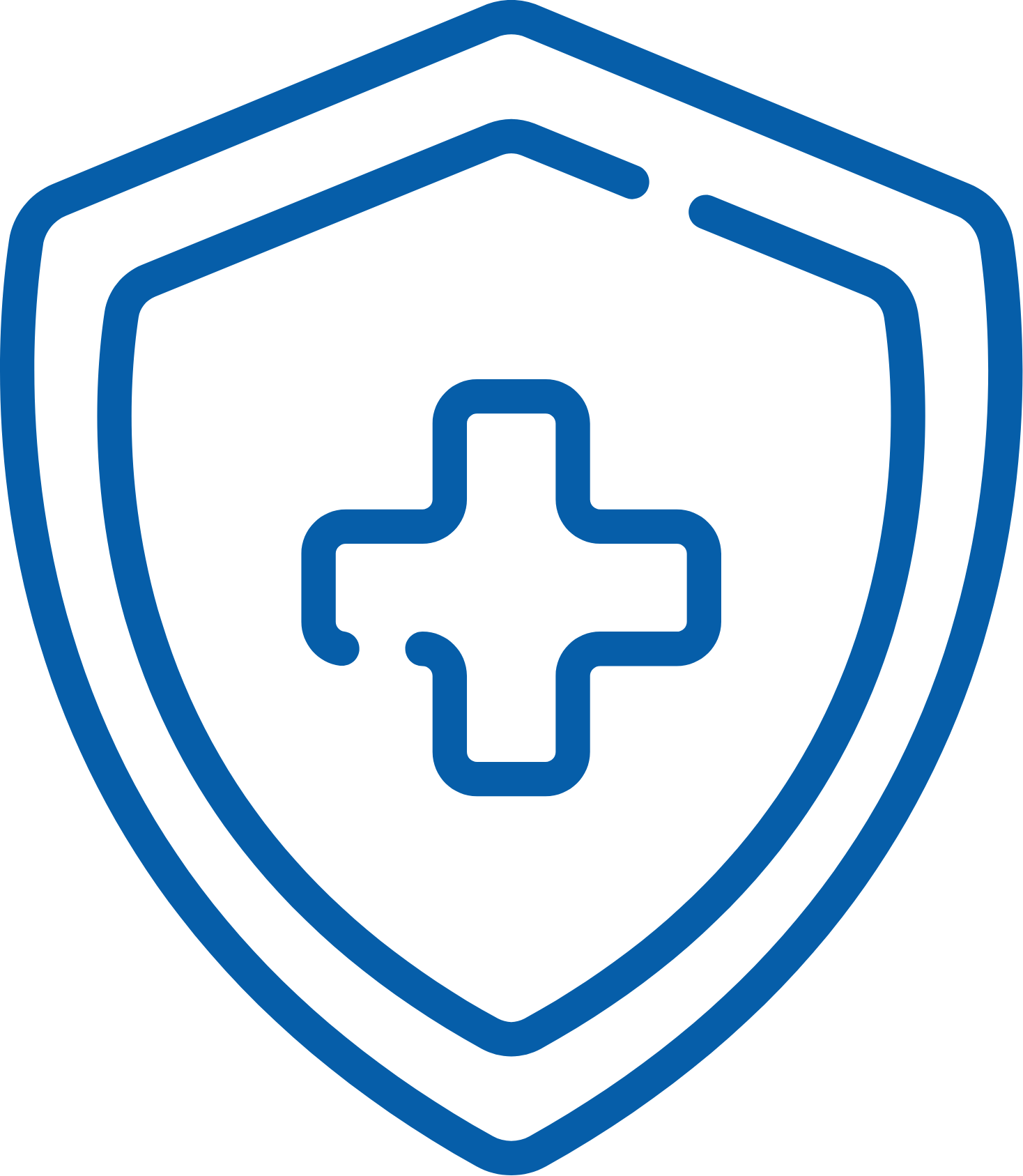