
Harness Fitting Part 1: Number & Type of Adjusters
July 12, 2013
When you’re shopping for something like oven mitts or beach towels, it’s generally safe to believe the tag that reads: “One Size Fits All.” But, when safety managers and other fall protection personnel are researching a full body harness for their employees, it’s critical to remember that “universal” sized harnesses are not always the best fit. One of the most important things about using a full body harness is ensuring that it is properly adjusted to the worker’s body. When a harness fits a worker improperly, it dramatically increases the chances that a worker will be injured or possibly even killed.
For those reasons, it is always prudent to review a worksite for elements that can influence the way that a harness fits a worker’s body. The most common factors that influence full body harness fitting are:
1. Number of Adjustment Points
2. Type of Adjustment Points
3. Working Conditions
4. Tool Requirements
5. Training
Each of these individual factors can have a profound impact on the fit of a full body harness. So, let’s explore these factors and how they influence the effectiveness of your harness.
NUMBER OF ADJUSTMENT POINTS
One of the things that can make a harness extremely dangerous is the number of adjustment points. If a full body harness only has THREE adjustment points, you should reconsider your purchase. Typically, three-point harnesses offer an adjustment area on both legs and one adjustment area across the chest. The reason that these harnesses are not as suitable for fall protection is because a worker will not be able to control the fit of the harness vertically. Without vertical adjustment options, there is more harness material that can be loose around a worker’s body. If the harness is loose when the worker falls, the worker will be at a significantly higher risk for falling out of the harness.
If a full body harness has FIVE points of adjustment, it will offer workers an opportunity to fit the harness to their body more effectively. Most 5 point harnesses have adjustment areas on both leg straps, two torso adjusters, and then an adjustment point across the chest. Having vertical adjustment options along the torso allows workers of all shapes and sizes to have a harness that fits securely.
TYPE OF ADJUSTMENT POINTS
Harness manufacturers tend to use two particular devices for leg and torso adjustment areas. Generally, the differences between those adjustment point devices are price and the quality of the fitting against the worker’s body. If the worker can’t adequately adjust the fit of the harness, the worker will be at a higher risk for equipment failure.
Leg Adjustment: Grommets vs. Quick Connect/Mating Buckle
There are many harnesses that use grommets for leg adjustments. Grommets are common because they provide reinforcement for the tongue buckle and they are less expensive for manufacturers. Many people who need to use a harness for limited amounts of time tend to prefer harnesses with this type of leg adjustment because they make the adjustment process a little faster. However, the number of grommets and the space between them limit how well the harness fits the worker’s legs. Depending upon the size of the worker, grommet leg straps may not offer a suitable fit.
Other harnesses will use an adjuster called a quick connect or mating buckle. This adjuster style is reminiscent of a seat-belt because there is a male-end and female-end that join together. This buckle makes it easier for workers to adjust the harness to their legs with a more customized fit. But, some workers are less inclined to use harnesses with this type of adjustment because they require a slightly longer amount of fitting time. If you’re worried about time efficiency on the job, the quick-connect buckle will require more time. But, if you have workers with dramatic size differences, the quick connect provides a better fit for a wider variety of people.
Torso Adjustment: Friction Buckle vs. Locking Cam
The biggest benefit to a harness that uses a friction-based adjuster is that the harness is more economic for manufacture and purchase. But, that lower price comes at a different cost. When workers need to make adjustments with a friction buckle, they will need to weave the harness webbing through the friction buckle in the appropriate way. If the worker doesn’t weave the web strap properly, they will be at a higher risk for falling out of their harness. As a result, workers will need time to carefully don their harness prior to performing their tasks. They will also need to undergo training to ensure that they learn the proper way to thread the webbing into the friction buckle.
The locking cam is definitely the more preferable type of adjuster for a few reasons. As the name implies, the cam has a locking mechanism on it that allows workers adjust the webbing and then lock the webbing securely into place. That added level of security creates a better fit for workers and reduces the likelihood that the harness will fail during a fall event. The design of the locking cam also allows workers to use one hand to make adjustments, which also leads to faster, more secure donning.
Next week, we will talk about the different ways that working conditions, tools, and training can have an effect on the way a harness fits a worker. Those three factors can get overlooked, but they are important because they can have a profound impact on the effectiveness of a worker wearing a full body harness.
Categories
Share this post
Let us help you
Contact us today to find the perfect product fit for your job
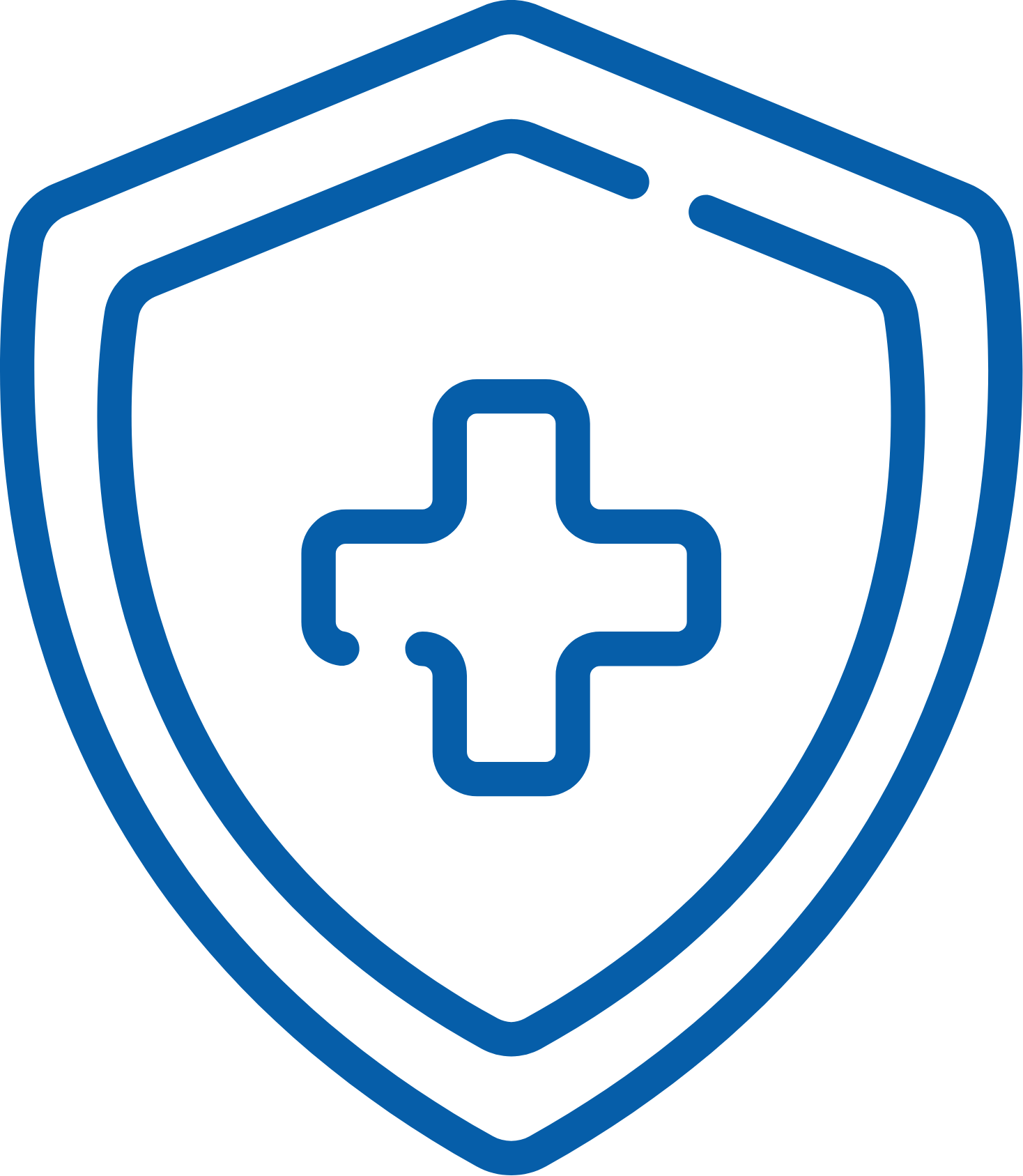