
Fall Protection: What to Do and What Not to Do
March 15, 2013
Whether you are the owner of a construction company, the foreman at a jobsite, or the safety manager on a factory floor, you all share a common concern about employee safety while performing tasks in the workplace. Worker safety is especially important when anyone is performing tasks at elevation. If you know that your employees are exposed to a fall hazard, it’s important for you to consider the different ways that you can go about protecting your workers from those hazards. Although fall protection can seem like an intense task, the following list will outline what you need to do to ensure that you have the proper fall protection system installed.
DO:
- Review OSHA 1910 for General Industry, OSHA 1926 for Construction, and ANSI Z359 to get familiar with different fall protection requirements. (NOTE: ANSI Z359 is the best resource for integrating a thorough fall protection program into the workplace.)
- Identify locations where workers may need to perform tasks at heights higher than 4 feet in General Industry or 6 feet in Construction.
- Perform a hazard analysis evaluation.
- Consult with a Qualified Fall Protection Engineer and a Structural Engineer about the best system to use based upon your location or application.
- Make sure that your system is installed properly in accordance with the manufacturer, Qualified Engineers, Structural Engineers, and the distributor who provided you with the system.
- Have your employees participate in a fall protection training course that is applicable to your system and facility needs.
- Teach your employees how to properly don a full body harness.
- Inform employees about the times and locations where fall protection is required.
- Perform routine maintenance and system checks on the equipment.
DO NOT:
- Ignore OSHA 1910, OSHA 1926, and ANSI Z359 requirements.
- Ignore performing a fall hazard analysis.
- Assume that people working below 6 feet are “safe” and can’t get hurt from a fall.
- Avoid attending a fall protection training course.
- Accept fall protection system or installation advice from anyone unless they have the proper certifications or many proven years of experience in fall protection.
- Allow uncertified persons to install your system.
- Assume that employees will figure out how to use the system properly.
- Assume that employees know how to use the fall protection system.
- Buy a fall protection system and not use it.
If you follow this list, you will find that the transition from not having fall protection to having fall protection will go more smoothly for both you and your employees. You will also find that you will have less down time if a fall occurs while boosting productivity with the confidence of knowing that a fall protection system is present.
Stay Safe!
Hannah Addison
Categories
Share this post
Let us help you
Contact us today to find the perfect product fit for your job
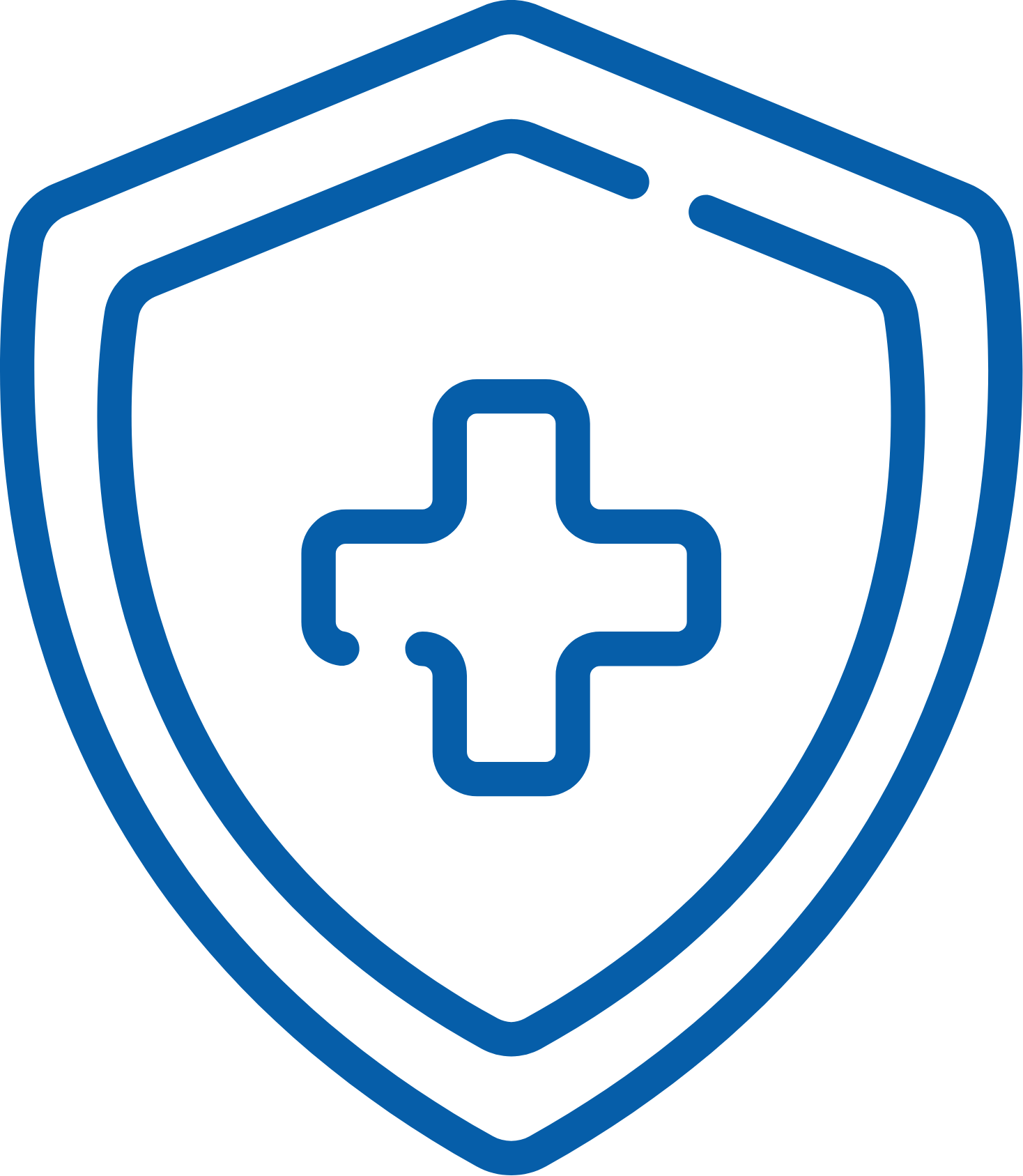