
Beyond Compliance: Creating a Culture of Safety
December 9, 2024
There are many safety regulations concerning fall prevention, including standards for fall protection systems, safety for workers at height, and more. OSHA 1910, OSHA 1926, and ANSI Z359 cover broad topics of fall prevention, and there are many specific standards within those regulations. These regulations define actions and steps employers must take to protect their workers from recognized hazards.
However, there is a difference between safety regulations and safety controls. Safety regulations are the laws employers have to follow regarding worker safety. Safety controls are the processes, practices, systems, and policies that an employer uses to reduce safety risks. Compliance with safety regulations can offer some safety controls, but there is more to managing workplace risks than just following the letter of the law.
According to the Bureau of Labor Statistics’ National Census of Fatal Occupational Injuries (CFOI), fatal falls accounted for 17 percent of all fatal workplace accidents in 2017. The NIOSH Fatality Assessment and Control Evaluation (FACE) Program investigates the causes and situations of workplace fatalities in different industries. The FACE Program found that between 1982 and 2015, 23 percent of construction workers killed in workplace accidents had access to fall protection equipment and failed to use it.
In the category of construction workers who had access to fall protection but didn’t use it, the employer was most likely compliant with the applicable fall protection regulations. These numbers demonstrate the disconnect between compliance and controls. But if an employer complies with the regulations, and the employees choose not to use the safety equipment, what other controls can be implemented?
A Workplace Culture of Safety
It starts with creating a culture of safety. A culture of safety depends on the understanding of a shared goal between employers and their employees, which is keeping workers safe and uninjured. It is important to understand that implementing safe work practices, such as a fall protection system, is a method of achieving that goal, and not a restriction placed on employees by an employer.
This approach is the opposite of the “safety cop” mentality, which is the idea that an employer will enforce safety policies just to make sure everyone is following the rules, or even just as a way to protect the employer from liability. The safety cop mindset puts employees and managers on opposite sides, and it can also make employees more reluctant to report unsafe work or workplace incidents.
Changing the Safety Cop Mentality
A way to address this mindset is to focus on the “what” instead of the “who” when it comes to safety. Employers will sometimes discipline a worker who is involved in a workplace safety incident, even up to termination. While this course of action is necessary in some cases, many incidents can be used to find and address shortcomings in a safety program.
Responding to an incident by focusing on what caused the incident, rather than who was involved, can often produce better results than disciplinary actions alone. Investigating the incident with the employee involved has the potential to help identify weaknesses in the safety program that can be corrected, which can help to reduce similar incidents in the future. Workers may also feel safer reporting incidents, near misses, or unsafe conditions, which can lead to additional improvements in the safety program. This kind of culture is especially important for work at height, since fall hazards increase the risk of serious injury or death. If workers believe that fall a protection system is there for legal compliance only, they might look for reasons to avoid using it.
The Role of Management
When a company’s leaders are invested in the personal safety of their employees, they can help create that culture. By being actively engaged with their workers and promoting personal safety, leaders can demonstrate that safety measures are implemented to protect workers from harm, not just to protect the company from OSHA fines and incident reports. This position is reinforced by giving workers the authority to stop working if they believe the work is unsafe. When management and employees share the common goal of personal safety, not just compliance, workplace safety can be improved.
The OSHA General Duty Clause requires employers to provide a workplace that is “free from recognized hazards that are causing or are likely to cause death of serious physical harm.” Providing fall protection for workers who are exposed to fall hazards achieves OSHA compliance, but a complete fall protection plan requires more than protective equipment. It also has to include all the elements that create a culture of safety. That culture can help lead to a more positive view of workplace safety overall and potentially reduce safety incidents.
5 Tips to Create a Culture of Safety
1. Make Safety Priority Number One
OSHA regulations and industry standards are in place for a reason, but compliance with the rules is only part of the picture. The rationale behind the rules—reducing risk and preventing injury—must remain priority number one. The establishment of such priorities starts with upper management. The less concerned a CEO is with risk reduction and fall prevention, the more difficult it becomes to encourage safe practices among the workforce. The message from management should be clear: “We care about your safety and well-being, so should you.”
2. Choose Proper Equipment
One key to promoting a culture of safety is choosing the proper equipment. Not only should that equipment appropriately address each fall hazard, but it should be easy to use, comfortable to wear, and easy to inspect. Many manufacturers are happy to work with you to select the most appropriate and comfortable fall protection gear for your facility.
3. Implement Training to Define Expectations
There needs to be a solid understanding of what procedures to follow on the jobsite. Workers can’t be expected to follow safety guidelines if they haven’t been properly trained. Maintaining up-to-date training courses for all employees ensures that everyone is properly acquainted with company expectations, such as fall protection training. Training should include everything, such as how to use equipment properly, safety precautions, and signs. Implementing safety training for new hires and refresher courses for tenured employees establishes a culture of safety early on.
4. Create Consequences for Unsafe Behavior
Whether they are rewarded or punished, having results for proper and improper adherence to safety standards will alter employee habits. Establishing a consequential system for breaking safety protocol will deter unsafe practices in the future. These consequences can range from probation, strikes in employee files, or even termination in extreme situations. Ultimately, there needs to be a zero-tolerance policy in place to hold violators accountable after they’ve completed documented training. Using such a system will enable workers to rectify bad habits, which puts an end to any possible liability.
Employees who violate safety protocols are not the only workers who should reap consequences. Reinforcing good behavior or safe actions with rewards will help correct bad habits as well. Encouraging your workers to not cut corners, wear vital PPE, and to complete their work safely will benefit everyone. Rewards can range depending on employer preference.
5. Encourage Safety Observation Reports and Feedback
Failure to report safety issues results in further problems. As it stands now, how many safety violations slip through the cracks because no one notifies management of the violations? Providing a convenient and accessible way to record problems on the worksite allows for more workers to voice their concerns. Who knows what’s going on better than the workers and operators in the field? Take advantage of your workers’ expertise and listen to them.
Create a committee for discussions and feedback. This committee should be developed from people on every level of your organization to guarantee a united front and understanding that these policies must be followed by everyone in the organization. With input from both the management and worker level, your culture of safety is self-correcting and constantly evolving. Your committee will hold the responsibility of managing training issues and researching new practices. Additionally, a safety committee will provide employees with a comfortable way to pass along suggestions.
Creating and maintaining a culture of safety is vital for the functionality of every workplace. From manufacturing to construction, whatever the industry, safety should always be the highest priority.
Categories
Share this post
Let us help you
Contact us today to find the perfect product fit for your job
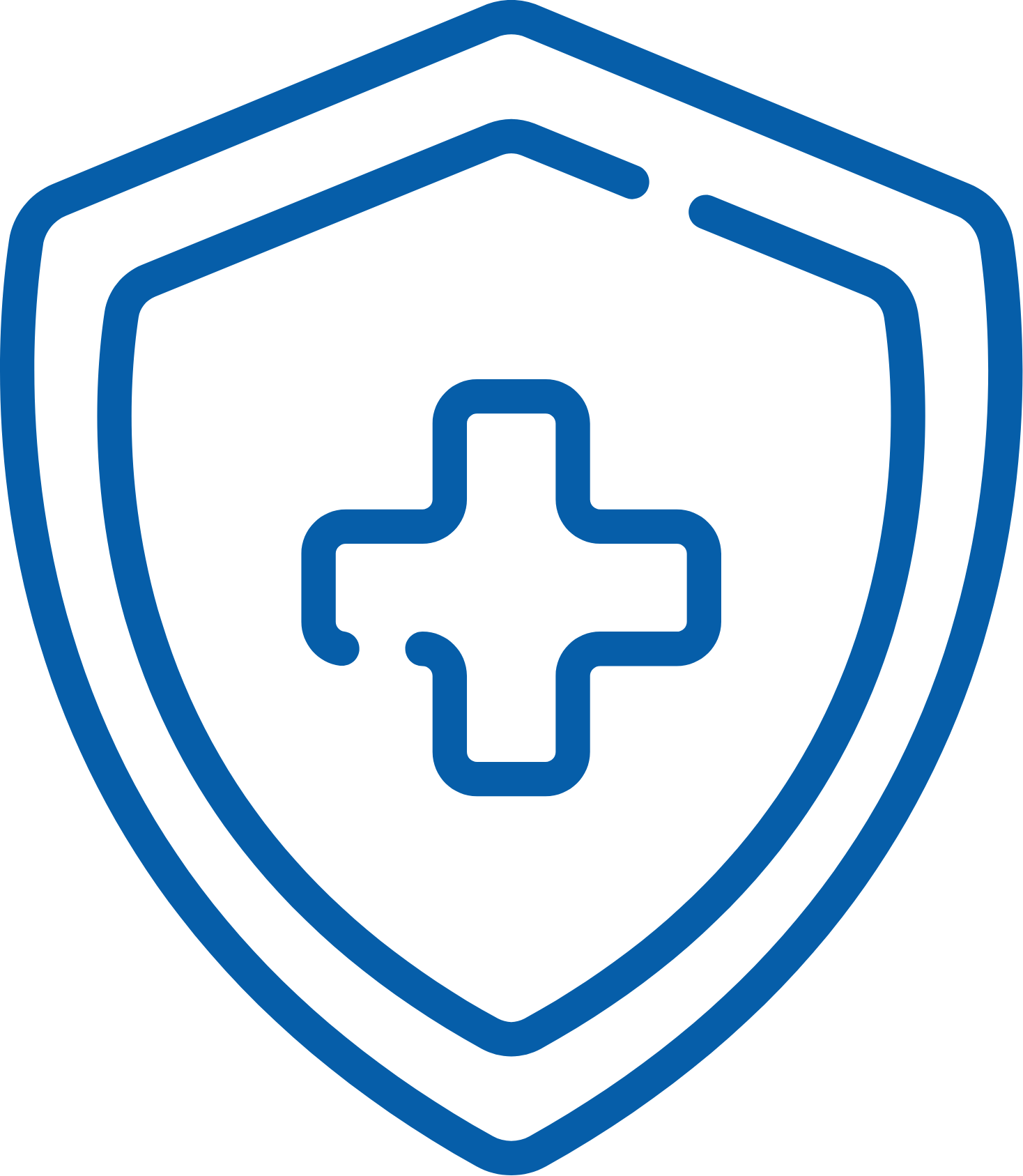