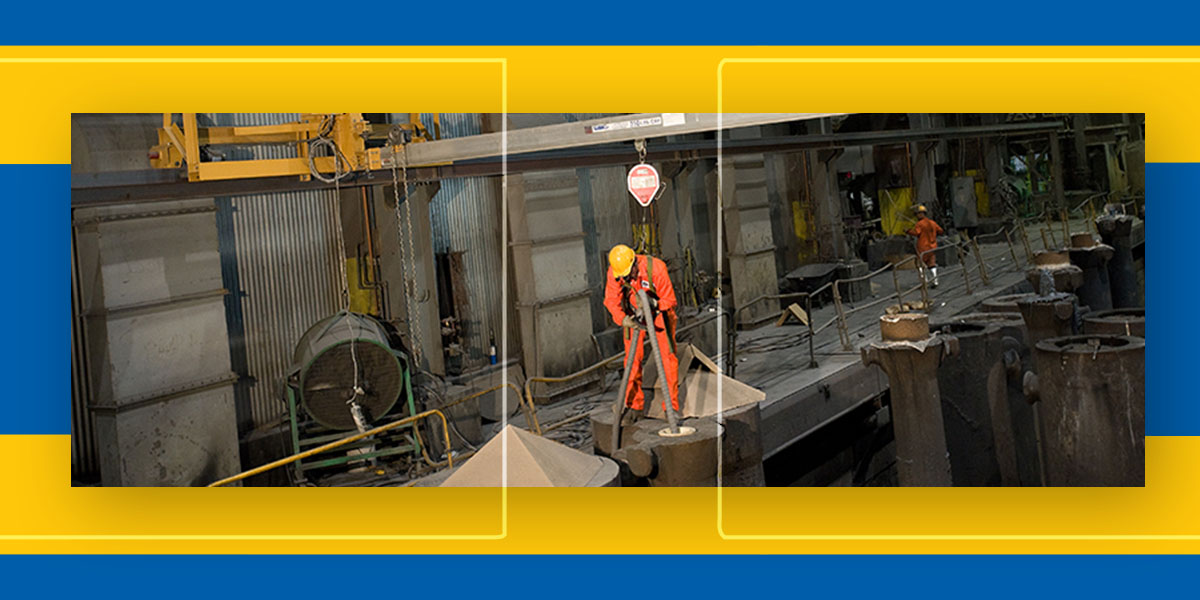
How Often Is Fall Protection Training Required?
May 1, 2023
The Occupational Safety and Health Administration (OSHA) requires competent person-level fall protection training. Employees working in maintenance facilities, manufacturing plants, railroads, and similar industries face the risk of falling and injuring themselves on the job. Falls can occur in various ways, including from scaffolds, ladders, roofs, and other elevated work surfaces.
That being said, it’s crucial that employers enforce proper safety protocols. Protecting workers should be a top priority in any industry. By training your staff on the Occupational Safety and Health Administration (OSHA) safety standards, you can reduce the risk of potentially life-threatening injuries from falls. This guide will cover everything you need to know about OSHA fall protection training requirements.
What Is Included and Covered in Fall Protection Training?
A comprehensive fall protection training program gives workers the necessary information to stay safe while working at heights. It should cover the following areas:
- OSHA and compliance, safety, and accountability (CSA) standards
- Hazards associated with working at heights
- How to prevent and control fall hazards
- Types of falls and their statistics
- Fall arrest and restraint systems, including lanyards, anchor points, harnesses, lifelines, and additional connectors
- Selecting the proper fall protection equipment for the job
- Correct descent techniques
- Emergency and rescue protocols
- Equipment maintenance and care
- Pre-shift visual safety inspections
Employers must ensure team members working at elevated heights have completed the fall protection course. An additional practical assessment may be required for equipment such as scissor lifts, boom lifts, and motorized scaffolds.
Furthermore, a qualified individual with fall protection certification should inspect each roof, ladder, scaffold, and any other elevated area before anyone uses it.
Here are three fall hazards the training course should outline.
1. Ladders
OSHA requires employers to provide fall protection for employees working on fixed ladders exceeding 24 feet. Employees should also understand and follow ladder safety protocols, including:
- Don’t walk under ladders.
- Avoid overreaching.
- Maintain three points of contact at all times.
- Ensure the ladder is on level ground before use.
- Lock the center ladder braces to secure it.
2. Roofs
Your staff should recognize fall hazards on roofs and use the proper fall protection equipment. Some important safety measures they should follow include:
- Ensure the harness fits and works correctly.
- Tie off and maintain a connection at all points.
- Confirm the safety of each anchor point.
- Identify and address risks like skylights, holes, and other roof openings.
- Don’t walk or sit on any roof openings.
3. Scaffolds
Suspension scaffolds should be tied or secured to prevent swaying. A personal fall arrest system, guardrails, or both must be provided for workers over 10 feet above a lower level. Employees should know how to set up and use scaffolds properly. Here are some safety guidelines to prevent falls from scaffolding:
- Scaffolds should be completely planked, have finished guardrails, and include proper plumbing and leveling.
- Workers should be able to access the scaffold safely and easily.
- A competent, fall-protection-certified person should inspect the scaffold before use.
- Never climb over a cross brace, stand on top of a guardrail, or use a ladder on the scaffold.
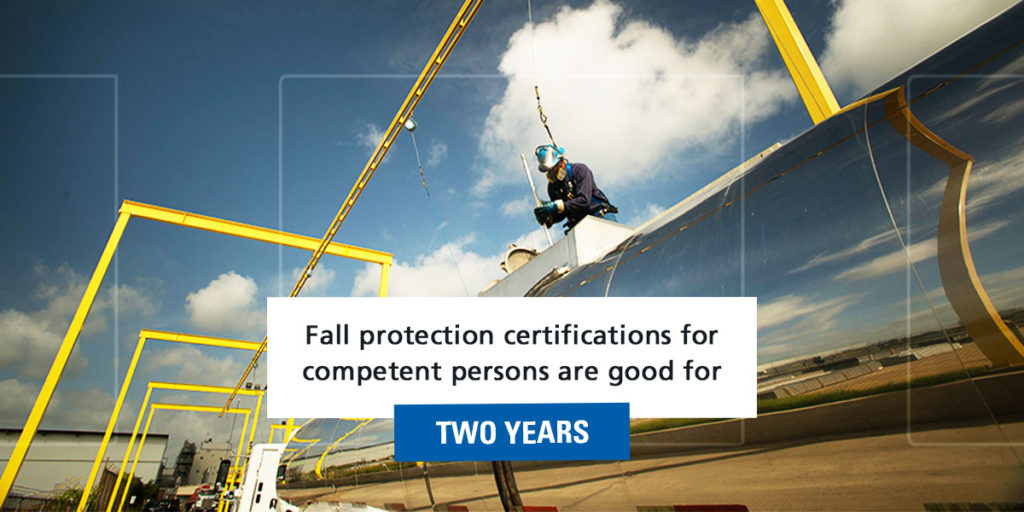
How Long Is the Training Good For?
Fall protection certifications for competent persons are good for two years. While authorized users aren’t required to renew their certification, certain circumstances warrant the need for a redo:
- Workplace changes render previous training obsolete
- Any trained employees don’t fully demonstrate the knowledge and skills to protect themselves
- Previous training is no longer relevant due to changes in fall protection systems or equipment
Your team could likely benefit from a fresh round of training if any of these situations apply. Employers are typically responsible for tracking re-certification requirements. Even if a team member has completed the course, the employer should use their best judgment to determine if the worker in question is qualified to work at heights.
How to Select the Perfect Trainer
An internet search for fall protection trainers may be quick and simple, but it can also yield hundreds of results, making it a difficult starting point. Referrals from an industry peer or professional organization tend to be more reliable.
After collecting referrals, read the training program descriptions to ensure they align with your organization’s needs. Then, reach out to the companies to inquire about their courses. Ask the provider about their training experience and any other questions you might have. Typically, it’s best to enroll in an on-site training program with hands-on practice.
A small student-to-instructor ratio is also ideal, as participants can receive more personalized, hands-on instruction for techniques and equipment. They can better understand how to install a fall protection system, put on and secure a harness, climb safely with a retractable lanyard, and more. Hands-on training can help build competence, knowledge, skill, and confidence in your workers.
What Level of Training Is Required?
There are four levels of fall protection training.
1. Awareness-Level Training
This training involves brief, on-site courses that give participants a rundown of fall hazards, fall protection systems, and how to use them. However, many experts don’t consider this true fall protection training, as it lacks hands-on equipment practice.
2. Authorized User Training
Authorized user training covers specific jobs and fall hazards workers will be exposed to. A best safety practice is to have any employee exposed to fall hazards complete authorized user training.
3. Competent Person Training
OSHA defines a “competent person” as someone who can identify existing and potential hazards in work environments and take the necessary measures to correct them. This training outlines a broad variety of fall hazards. Workers who undergo competent person training — typically supervisors — should understand all fall risks and protection methods.
These individuals require a higher level of training since they must be able to inspect equipment, evaluate fall hazards, and address them accordingly. They also must recognize when employees are working in hazardous conditions, like on an elevated platform with no fall protection, or misusing equipment.
4. Qualified Person Training
Generally, people who undergo qualified person training have specialized degrees or training qualifying them to address technical situations, like designing horizontal safety systems or making certified anchorage points. An employer should appoint someone with extensive fall protection training and knowledge as “the qualified” person. This goes for authorized and competent persons, as well.
Regardless of the certification level, fall protection training helps employees understand and recognize different fall hazards and how to prevent and approach them.
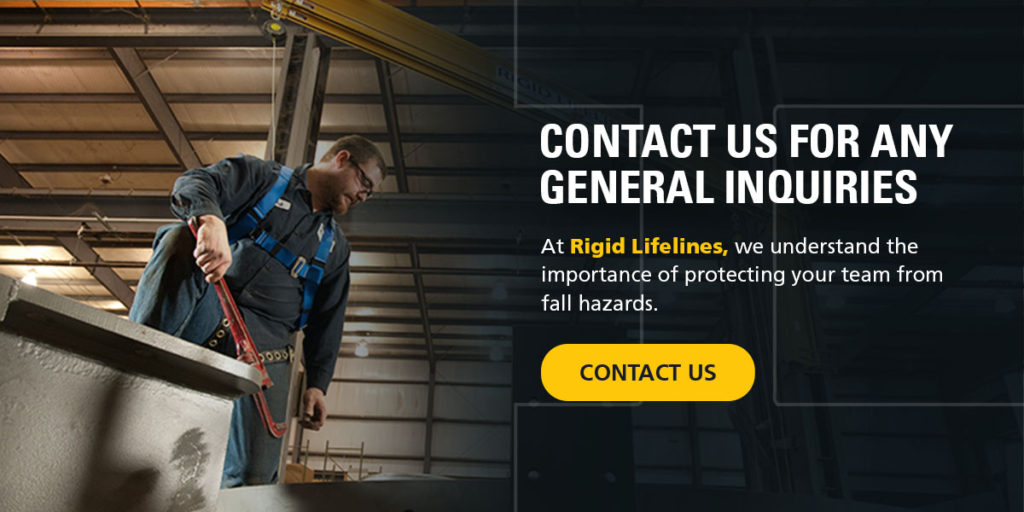
Contact Us for Any General Inquiries
At Rigid Lifelines, we understand the importance of protecting your team from fall hazards. We have an extensive selection of overhead fall protection solutions to make your operations safer.
Whether permanent overhead systems or portable fall arrest equipment for fluid operations, we can help point you to one of our standard systems or customize one to your needs. Contact us today to inquire about our fall protection systems or general safety standards.
Categories
Share this post
Let us help you
Contact us today to find the perfect product fit for your job
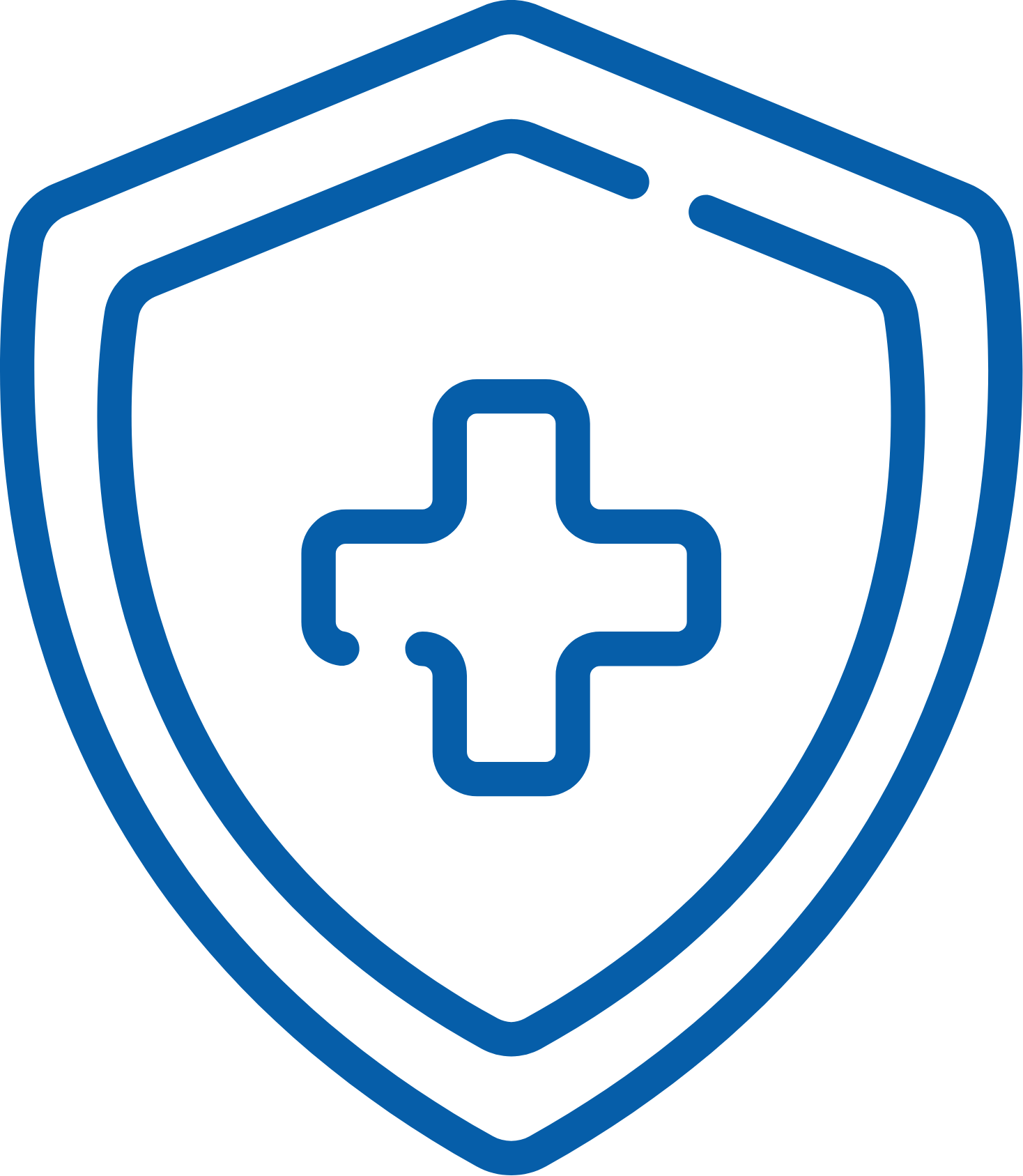