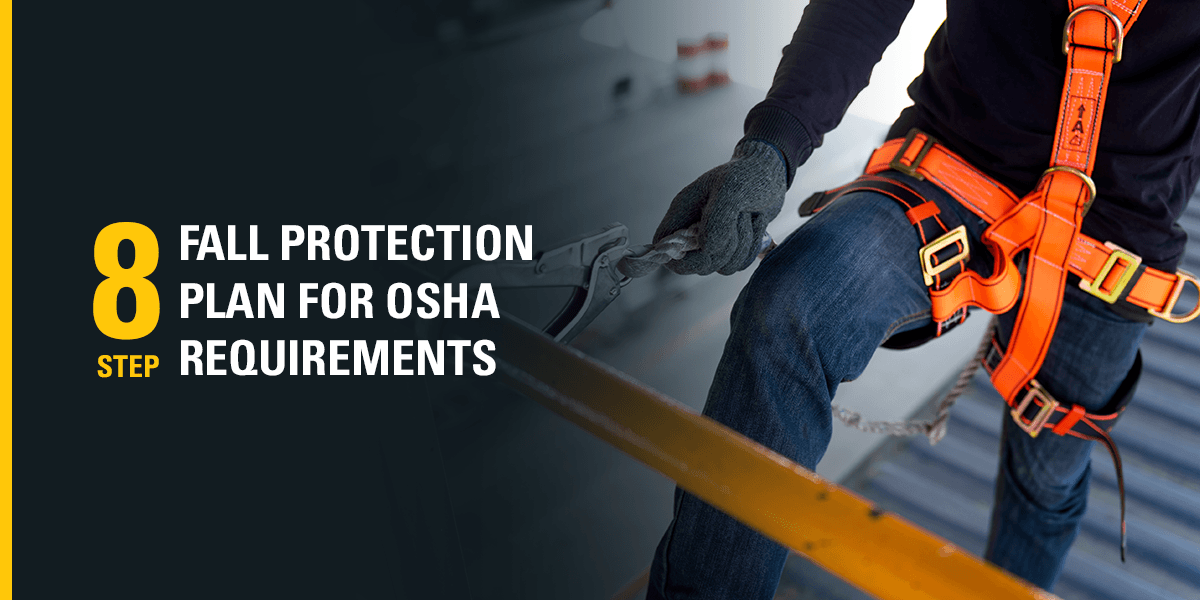
8-Step Fall Protection Plan for OSHA Requirements
March 7, 2022
Potential falls in the workplace are among the most dangerous threats faced by employees. The World Health Organization (WHO) reports that almost 2 million workplace-related deaths occur each year, with occupational injuries responsible for 360,000 deaths. Construction companies, contractors, and other employers have no higher responsibility than to the safety of their employees and colleagues.
Having a comprehensive fall protection plan in the workplace is of the utmost importance for employers in the construction industry. A fall protection plan helps protect all employees’ health and safety. Additionally, Occupational Safety and Health Administration (OSHA) compliance can help save businesses money by preventing fines and reducing insurance costs and injury compensation claims. Some experts suggest that having a solid safety plan can increase productivity and decrease workers’ stress and perceived risks in the workplace.
8 Steps for Creating an OSHA-Compliant Fall Protection Plan
Created as part of the Occupational Safety and Health Act of 1970, OSHA and all its rules and regulations exist to ensure safe, healthy working conditions for all workers. It does this by setting and enforcing safety standards and implementing these guidelines through training, education, outreach, and other forms of assistance.
OSHA coverage applies to nearly all public sector workers throughout the 50 states and other jurisdictions, including Washington, D.C., Puerto Rico, the Virgin Islands, American Samoa, and Guam, and others. For most businesses, particularly those in the construction industry, a detailed, written fall protection plan is one of the best and most important ways to ensure OSHA compliance in your workplace. By extension, you protect the health and safety of all workers and employees.
Construction sites can be among the most hazardous working environments, and falls are among the deadliest events in these settings. Fall prevention measures are a key component of workplace safety. Many construction managers who create workplace safety plans dedicate significant time and energy to forming a written strategy for fall protection and prevention.
While there are different ways to approach workplace safety strategies, the following eight steps can be great guidelines for crafting a fall protection plan that meets OSHA requirements.
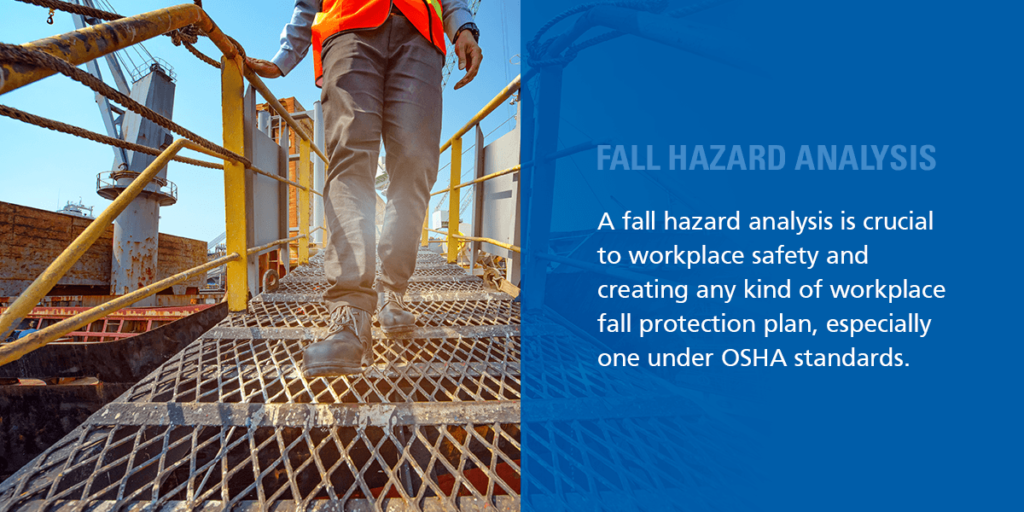
1. Fall Hazard Analysis
A fall hazard analysis is crucial to workplace safety and creating any kind of workplace fall protection plan, especially one under OSHA standards. All employers have a serious duty to their employees and colleagues to create workplace environments that are as safe as possible for the people who spend time in these settings. A fall hazard analysis—sometimes called a fall hazard survey—is often the first step to creating a meaningful fall protection plan.
A fall hazard analysis begins with identifying all real and potential fall hazards on the site. In addition to locating these hazards, the fall hazard analysis must account for the types of risks identified, along with the physical form of the hazard. The analysis should note the frequency with which workers may contact each hazard and for how long. Lastly, the fall hazard analysis must also evaluate each fall hazard’s height and the worst-case scenarios if a fall occurs.
During the analysis process, depending on the exact characteristics of the workspace in question, there may be some additional environmental factors to consider. Some common, additional environmental considerations can include the presence of:
- Chemicals.
- Fires and fire-prone materials.
- Sharp and abrasive materials and equipment.
- Moving walkways and unstable walking surfaces.
A thorough analysis of all existing fall hazards is perhaps the most critical step for creating a fall protection plan that addresses these hazards in both practical and efficient ways.

2. Pre-Planning for Fall Protection Systems
Business owners, managers, and construction contractors all play a role in protecting the workers they employ and, in some cases, work alongside on construction sites. To create and maintain OSHA-compliant workplaces, business owners and managers must institute safety standards and protocols that ensure the highest possible safety for all workers.
To do so, business owners and managers should first consider the existing safety policies and procedures for their businesses. In many cases, existing safety policies can offer considerable guidance and solutions for fall hazards in the workplace. Once owners and managers have identified and evaluated existing safety plans and their effectiveness or lack thereof, managers can create comprehensive fall protection plans and systems that will meaningfully address safety and fall prevention in their workplaces.
This stage of pre-planning should also consider the long-term needs and goals of the fall protection systems, including ongoing responsibilities such as maintenance, inspections, record-keeping, incident reporting, enforcement of standards, training courses, education, and equipment repairs and replacements as needed.
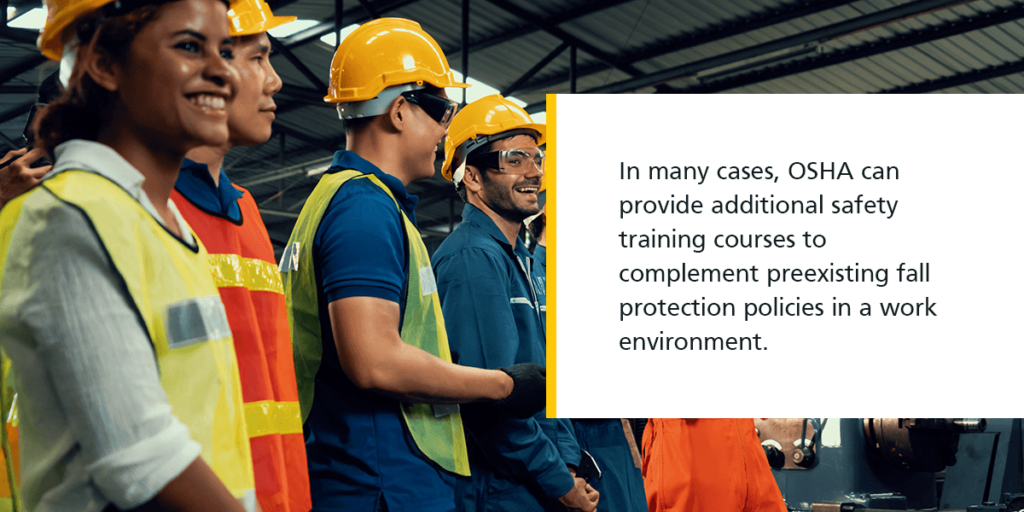
3. Policy Development
Developing and implementing an effective fall protection policy will depend on several factors. Business owners, managers, and contractors have a solemn duty to ensure their workers’ and colleagues’ safety, health, and security throughout the workplace. Some things to consider during policy development may include investments in OSHA training and educational programs, material investments in guardrails, and other safety equipment.
During the policy development stage, business owners and managers should carefully consider all factors necessary to prevent falls in the first place and rescue plans in the unfortunate event that a fall should occur. Some of these factors include:
- Site-specific fall hazards.
- The type of fall protection to use, like guardrails, nets, and anchor points.
- Ongoing inspections of both new and existing equipment.
- Availability of first-aid care.
- General rescue procedures.
Once the business owners and managers have made all necessary decisions and developed their policy for fall prevention, they must codify the policy and plans in written form and communicate it to employees, employers, and all other workers in a language that each person can understand fully. In many cases, OSHA can provide additional safety training courses to complement preexisting fall protection policies in a work environment.
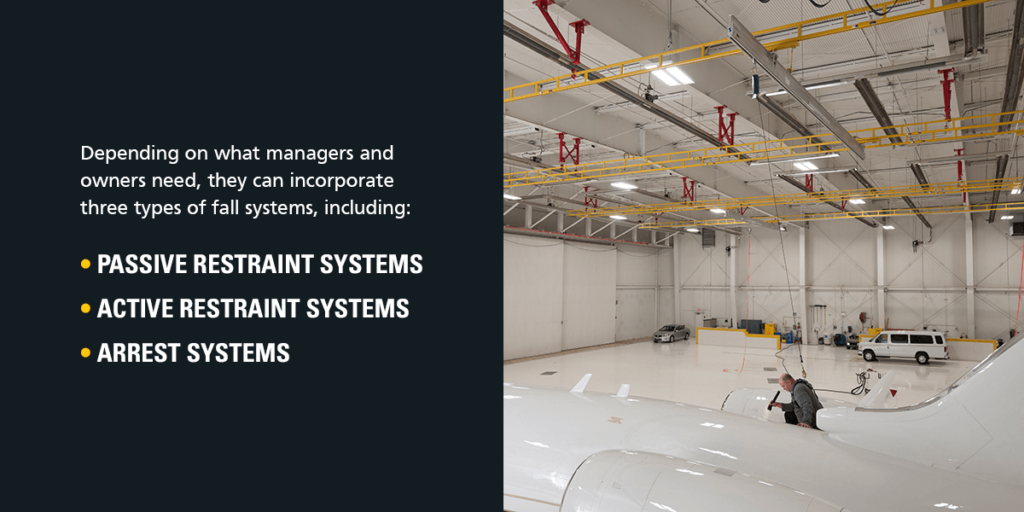
4. Fall Protection System Selection and Installation
The selection of an appropriate fall protection system and its installation will depend on variables specific to each workplace and the specifics of each fall hazard in question. OSHA publications, such as their “Model Fall Protection Plan,” can offer invaluable guidance and insight into how best to select and implement an effective, compliant fall protection system. Business owners, managers, and employers can reach out directly to their local OSHA office for additional guidance and assistance.
When choosing the right fall protection system, you can select between many types of available setups. Each system offers a unique way to protect your employees from fall hazards. Systems will fall under two categories: fall restraint or fall arrest. Restraint systems help prevent falls by using equipment to eliminate fall risks by restricting access to areas where workers could fall, while arrest systems use equipment to arrest a falling worker before he or she reaches a lower level. Both types of systems are important for workplaces to thoroughly protect employees from fall risks and injuries.
Because business owners and managers carefully consider where fall hazards exist at their workplaces during fall analysis and other previous steps, they can then look at those types of risks to determine which systems to integrate. Depending on what managers and owners need, they can incorporate three types of fall protection systems, including:
- Passive restraint systems: Passive restraint systems are preventive measures and permanent fixtures that remain in place to protect employees after installation. The most common passive restraint feature is a permanently installed guardrail.
- Active restraint systems: While passive restraint systems don’t necessarily require interaction from workers, active restraint systems use gear employees can wear to limit their movement while they work. A common type of fall restraint is a tie-off system that allows a worker to reach a leading edge and move side-to-side without going over the edge.
- Fall arrest systems: Fall arrest systems stop falls while they are occurring. Employees must use fall arrest equipment each time they enter fall risk zones, and regularly inspect equipment to ensure it is safe to use when needed.
After determining what types of systems will best benefit and protect your employees, you can then go ahead and install equipment. Since you have already identified higher-risk areas, you can install which system will ensure optimal worker safety in each risk zone.
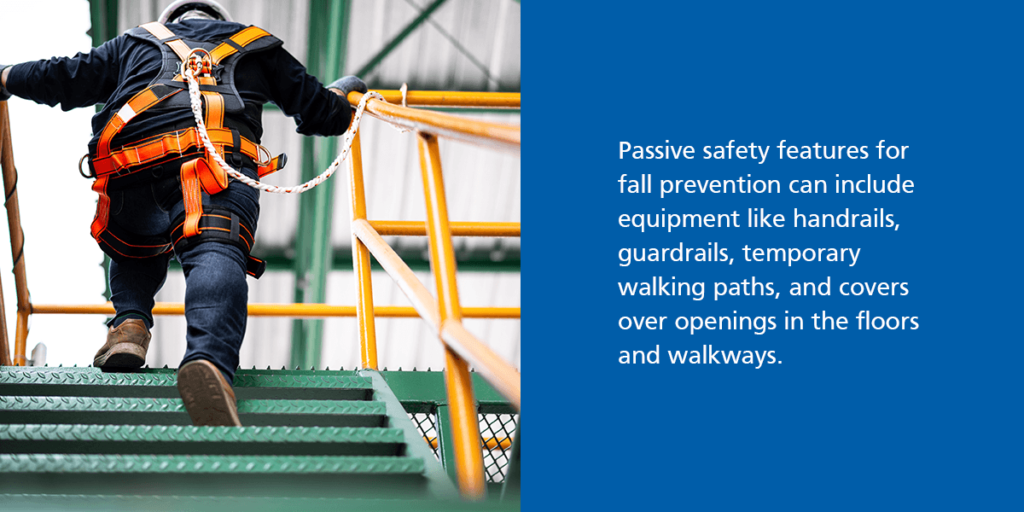
5. Planning Methods of Control and Fall Procedures
In nearly every case, the most effective type of control is one that allows workers to avoid the fall hazard entirely. If complete avoidance of the fall hazard is not possible for whatever reason, then the standard industry recommendation usually advises the introduction of passive safety features.
Passive safety features for fall prevention can include equipment like handrails, guardrails, temporary walking paths, and covers over openings in the floors and walkways. In some cases, you can also use safety netting as a passive method to prevent fall-related deaths and injuries.
If passive safety features are not an option to mitigate the risk of existing fall hazards, the workplace must provide adequate fall arrest systems for all workers. Complete fall arrest systems may include full-body harnesses, self-retracting lanyards, energy-absorbing lanyards, and other equipment.
Fall arrest systems require workers to complete training in order to ensure maximum safety. Rigid rail systems also provide the required anchor points for workers to connect to. Consequently, it is crucial that all workers who are trained to use the fall arrest systems know how to perform inspections before each use. All arresting equipment must undergo regular, ongoing maintenance and repairs. Routine maintenance and repair are also crucial to ensure the effectiveness of passive safety features.
Even when workers are careful, falls in the workplace are still possible. As such, any fall protection plan will also account for rescue policies and procedures should a fall occur. Fall rescue plans should consider both who will perform the rescue and what equipment and methods are at the location of each fall hazard.
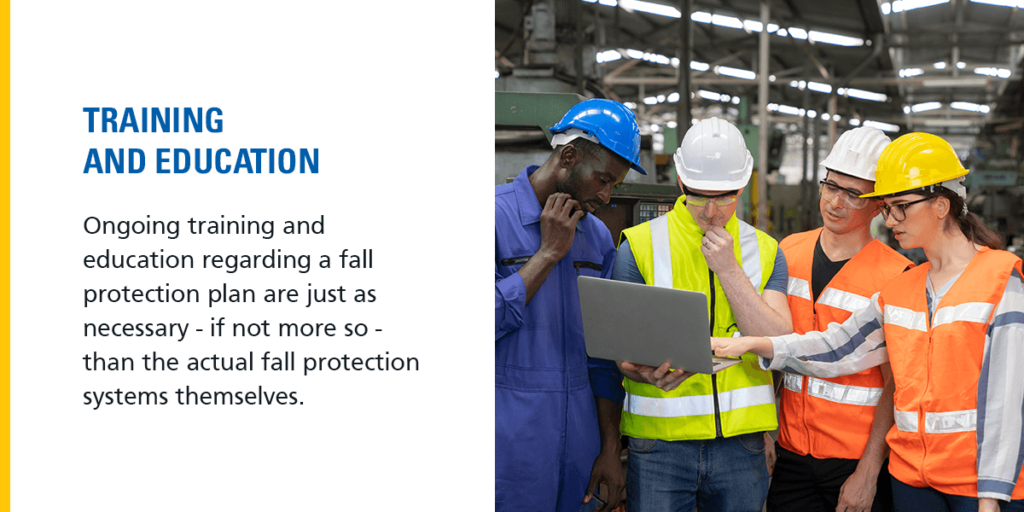
6. Training and Education
Ongoing training and education regarding a fall protection plan are just as necessary as the actual fall protection systems themselves. Simply making all workers and employers alike aware of the inherent risks and dangers in the construction site can go a long way in raising consciousness and interest around the topic of worksite safety and fall prevention.
These training courses can include classroom instruction—especially for workers who regularly encounter fall hazards as a part of their daily work. In fall protection training, both employers and workers can learn invaluable skills and procedures for mitigating the risk of falls and thus fall-related injuries and deaths by extension.
Through ongoing training and educational offerings, workers on all levels of the hierarchy should have a thorough knowledge of all fall prevention systems—including both passive and active safety features, rescue plans, safety clothing and equipment, and OSHA regulations and standards, among other considerations. In addition to classroom training, hands-on workplace training is also key to ensuring the effectiveness of fall protection plans when employees put them into action in the real world.
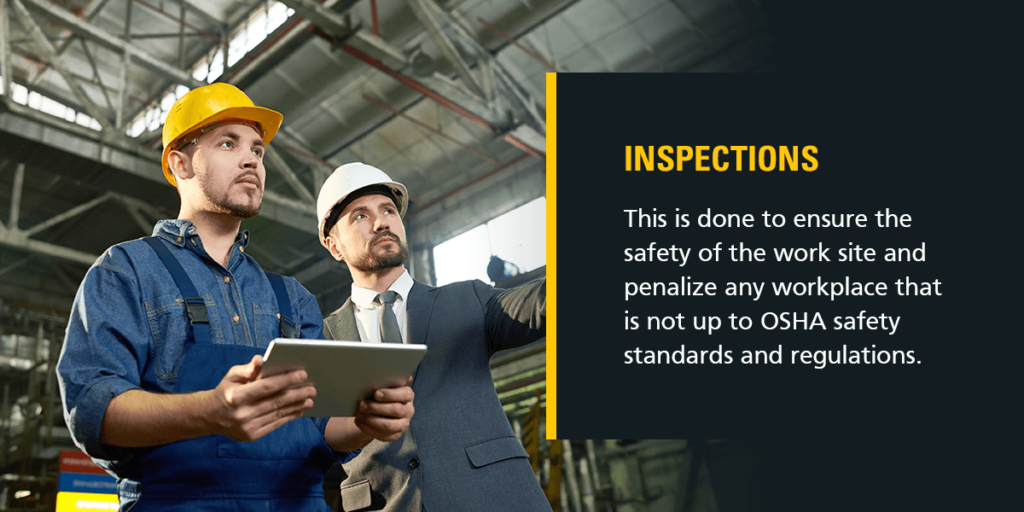
7. Inspections
In many cases, OSHA will perform on-site inspections. This is done to ensure the safety of the worksite and penalize any workplace that is not up to OSHA safety standards and regulations.
A workplace’s failure to meet OSHA standards may result in hefty fines—as of 2021, the maximum penalty amount was over $13,000 per violation. If you receive an OSHA violation, it is crucial to address and solve the issue as soon as possible because fines rise for repeating offenses to over $135,000 per unfixed violation.
Because OSHA has so many worksites to review each year, they prioritize higher-risk sites with more worker complaints and reports of injuries. They review the inspection history of each workplace before conducting inspections, and any existing or past violations will appear in this history. If you have existing violations, you will also rise on the priority list, so it is in the best interest of owners and managers to quickly and efficiently address violations and establish a fall safety plan.
As such, it greatly benefits any business owner, manager, or contractor to ensure that their workplaces meet OSHA safety standards at all times—both out of duty to their workers and due to financial considerations.
8. Ongoing Audits and Continual Improvement
Even though OSHA conducts regular inspections and audits, these reviews will not be the only ones companies face. Employers have a duty to conduct regular inspections of all worksites and equipment to ensure the proper and effective implementation of their fall protection plans and policies. Checks give crucial insight into the effectiveness of existing safety and fall protection plans.
Owners and managers should establish schedules for regularly inspecting and testing the effectiveness of all protective equipment, especially gear that employees wear directly, like active restraint and fall arrest gear. When you routinely ensure equipment functions at its best, you can prevent injuries or deaths resulting from faulty or broken gear.
Because business owners and managers can identify the limits of their existing plans during inspections and audits, they then have the information necessary to make adjustments and improvements to their fall protection plans as needed. By ensuring that all fall protection plans are as up-to-date as possible and actively understood and rehearsed by workers, employers can greatly improve overall workplace safety.
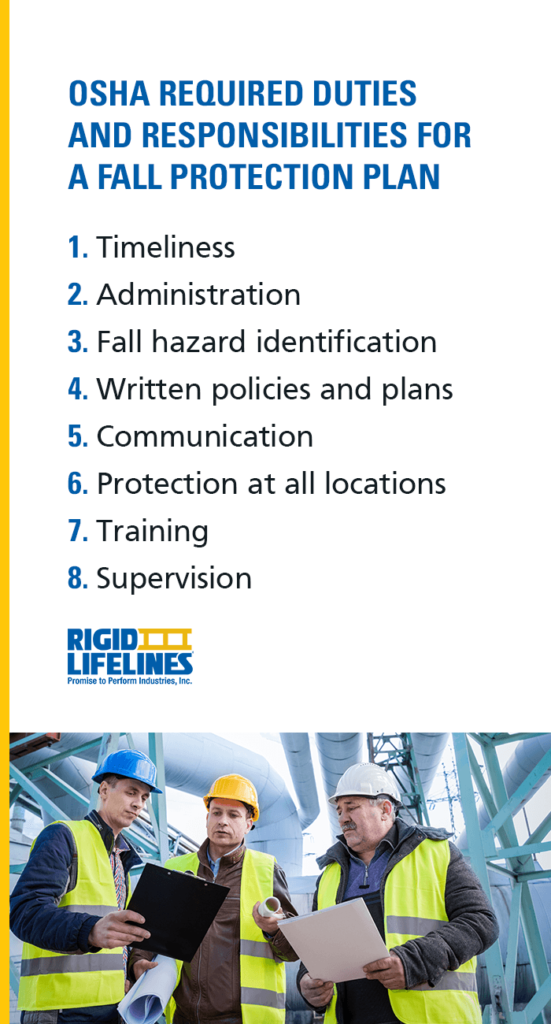
OSHA Required Duties and Responsibilities for a Fall Protection Plan
ANSI Z359.2-2007 is a private fall safety and protection standard that establishes the minimum requirements for a thorough fall protection program that covers many different risks in the workplace to create safer environments for employees.
This standard includes a sample policy statement that employers can use as a basis for their fall protection programs. However, it is critically important that each business develops a unique policy and program to best meet the specific needs of company employees and fit best with their current equipment and structures. Still, the ANSI policy statement is a great guide for employers and managers to use as a starting point to help determine what they might need to include and cover.
Despite being a privately-developed standard, ANSI Z359 can be cited by OSHA under the General Duty Clause or through Incorporation by Reference of any portions.
The American National Standards Institute (ANSI) lists eight required responsibilities for employers, owners, and managers to conduct to meet the basic necessities of workplace safety for fall risks and injuries, which include:
- Timeliness: Employers are responsible for providing resources required to carry out and support all aspects of their fall protection program quickly and efficiently so the right teams can install and use them.
- Administration: Employers need to appoint a staff member to administrate their fall protection program across the company. This person must have the necessary background information, experience, and training to lead and train other employees effectively. Further, they should also possess abilities to judge the effectiveness and safety of the program and equipment.
- Fall hazard identification: Employers are responsible for continually protecting employees from any fall hazards they could encounter in the workplace. To do this, they need to evaluate workplace environments and equipment regularly to identify existing and new fall hazards. Afterward, they are also responsible for correctly documenting and implementing policies to rid the workplace of hazards.
- Written policies and plans: Employers must thoroughly outline fall protection and rescue procedures for every workplace where they use a fall protection system to prevent and reduce fall risks. Written outlines are necessary to help employees and managers understand and easily access protection and rescue procedures at their individual locations.
- Communication: Employers need to communicate with all authorized personnel about any potential fall risks before entering work environments. This communication standard includes all work locations the employer owns and operates.
- Protection at all locations: Employers need to choose and install systems that include adequate equipment for all work locations, including outside areas where employees may travel. Employers must properly train all employees to recognize fall risks so that they can better avoid them. For outside locations, business owners can work with site employers to best protect visiting employees and provide them with comprehensive fall protection.
- Training: Employers need to train all employees in understanding fall risks and operating all fall protection systems they will encounter and use in their workspace.
- Supervision: Employers must include authorized and trained personnel to supervise locations with fall risks and protect employees using fall prevention equipment. These experienced individuals can ensure all employees are following company guidelines and using equipment correctly.
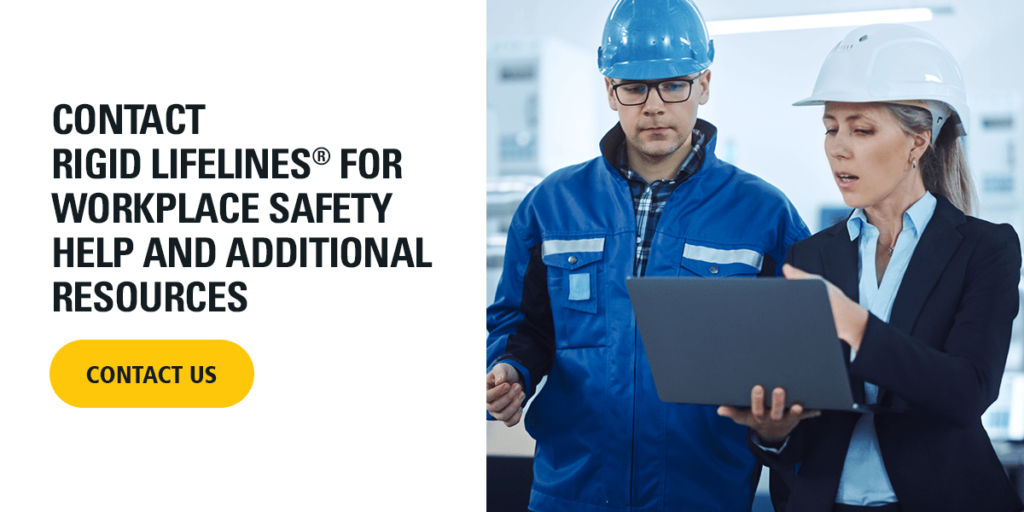
Contact Rigid Lifelines® for Workplace Safety Help and Additional Resources
With over 20 years of experience, Rigid Lifelines® is a proven industry leader in workplace safety and fall protection systems. We specialize in engineering, designing, and testing rigid rail fall arrest systems. All of our products comply with OSHA 1910, OSHA 1926, and ANSI Z359 standards, and we’re proud to offer best-in-class solutions for fall prevention and overall workplace safety.
Our experienced team of designers and engineers dedicate themselves to helping your business and workplace find the best safety solutions. Driven by research and a mindset of safety and service, we are ready to assist you in every possible way. Contact Rigid Lifelines® today to learn more.
Categories
Share this post
Let us help you
Contact us today to find the perfect product fit for your job
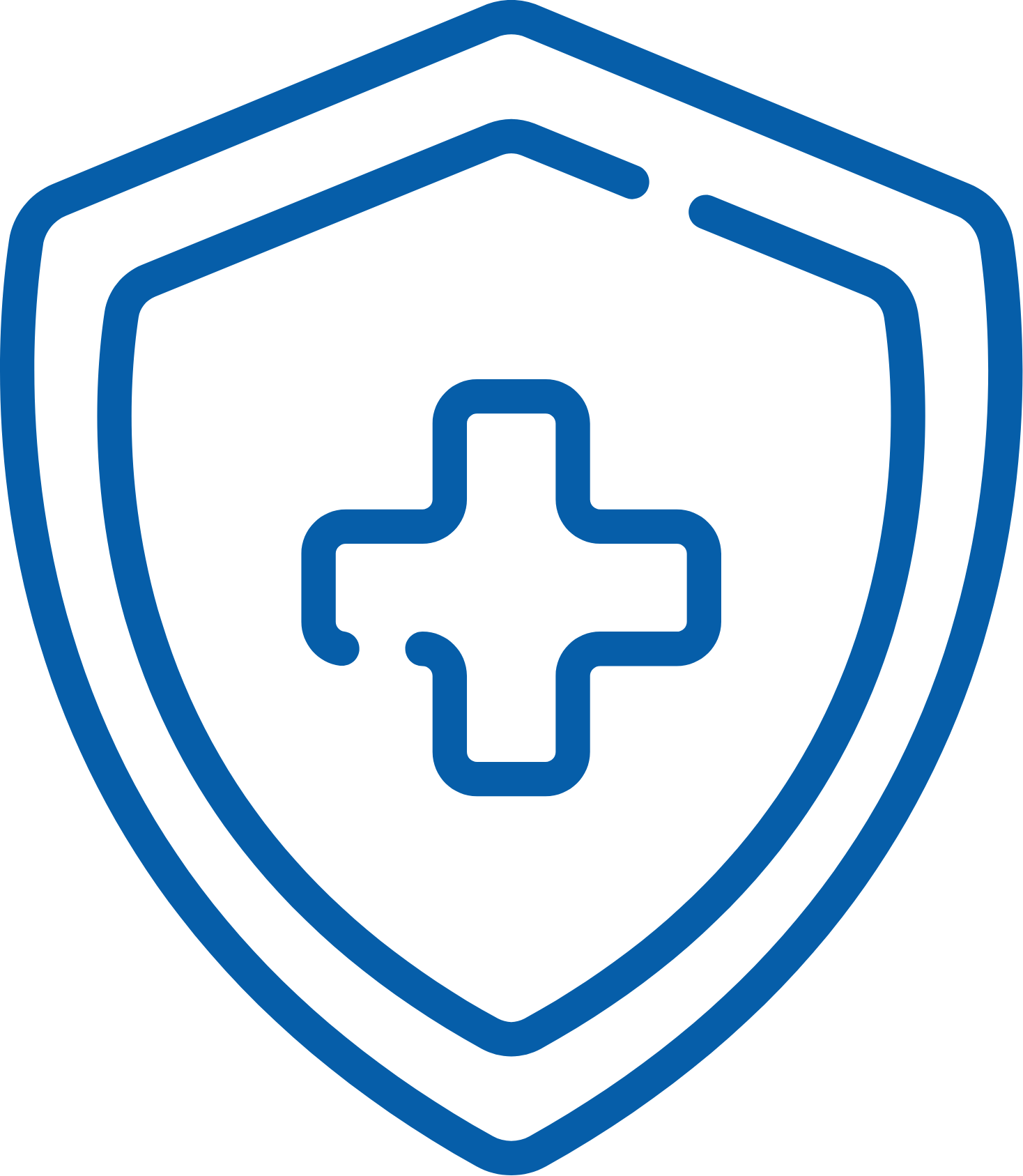